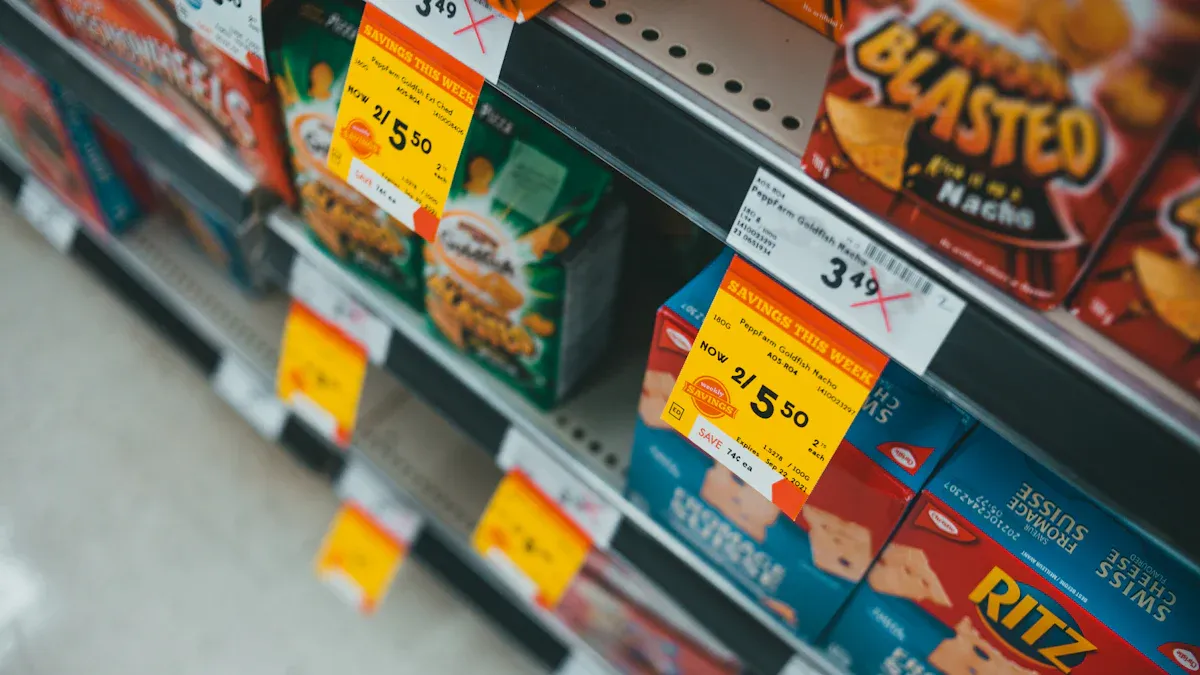
Retailers face unique challenges in refrigerated grocery sections, where rapid price changes and accuracy are essential. Electronic price tag systems, including Electronic Shelf Labels and ESL Price Tag solutions, enable real-time updates and reduce manual errors. Many stores report that digital price tags, managed through ESL Gateway AP, improve operational efficiency and compliance. Esl Retail environments benefit from automated pricing and inventory alerts, while waterproof electronic tags withstand cold, moist conditions. Staff productivity rises as employees shift focus from paper tag replacement to customer service, driving greater efficiency and smoother price changes.
Overcoming Refrigerated Retail Challenges with Electronic Price Tags
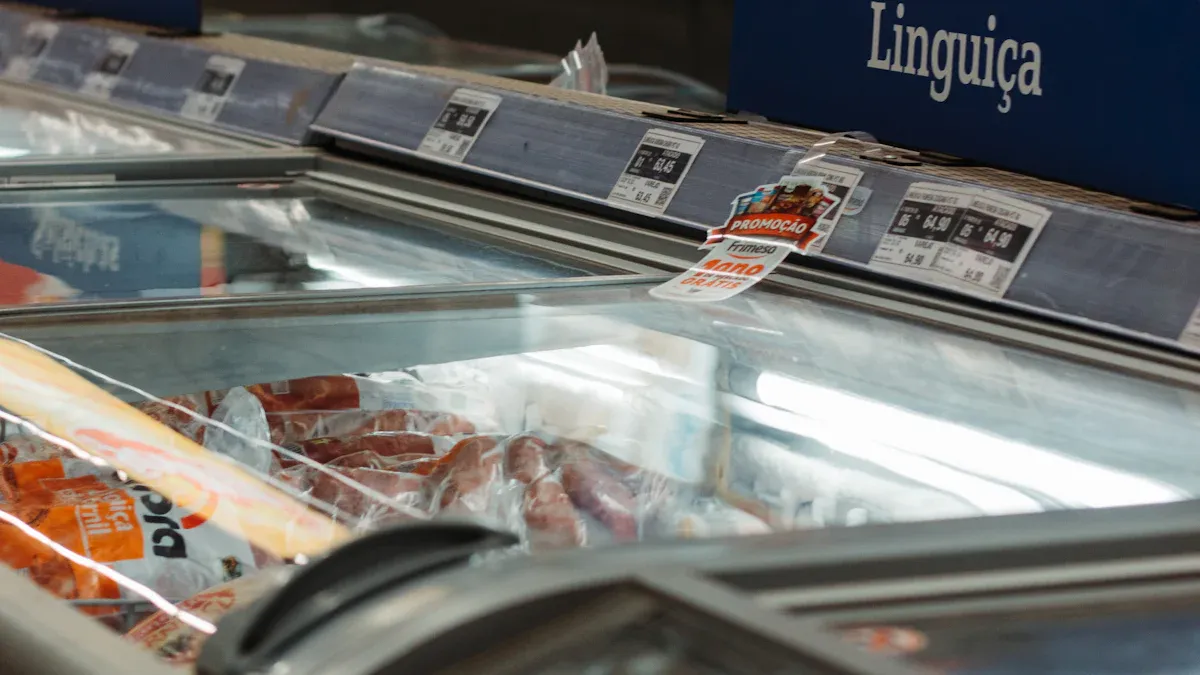
Temperature and Moisture Issues in Grocery Environments
Impact on Traditional Paper Tags
Grocery retailers often struggle with environmental conditions in refrigerated and frozen sections. Temperature and moisture fluctuations can quickly degrade traditional paper tags. When exposed to condensation or frost, paper labels lose legibility and adhesive strength. This leads to frequent replacements and increased labor costs. In contrast, digital price tags with environmental protection ratings, such as IP65, resist dust and moisture. These tags maintain performance and visibility even as temperatures shift from coolers to freezers. For example, the HS290 digital price label operates reliably between 0 and 40°C, making it suitable for grocery environments where conditions change rapidly. Traditional tags lack this resilience, resulting in reduced lifespan and inconsistent pricing information.
Risks of Manual Labeling in Cold and Moist Conditions
Manual labeling in refrigerated grocery sections introduces several risks. Employees must enter cold aisles repeatedly to update prices, which increases the chance of errors and exposes staff to uncomfortable working conditions. Moisture can cause handwritten or printed labels to smudge or detach, leading to confusion for customers and staff. These issues become more pronounced in a frozen environment, where frost and condensation accelerate label deterioration. Electronic shelf labels eliminate these risks by providing clear, tamper-resistant displays that withstand harsh conditions. Staff can update prices remotely, reducing time spent in cold areas and minimizing mistakes.
Compliance and Pricing Accuracy
Food Safety and Regulatory Requirements
Grocery retailers must comply with strict food safety regulations. Perishable foods require storage at or below 41°F to prevent bacterial growth. Freezers and refrigerators need accurate thermometers, regular calibration, and detailed temperature logs. Staff training on hygiene and temperature monitoring remains essential for compliance. Real-time monitoring systems track temperature and humidity, providing instant alerts if storage conditions deviate from safe parameters. Automated record-keeping supports compliance with regulations such as the Food Safety Modernization Act (FSMA) by offering accessible digital logs for audits and inspections. These measures help grocery stores maintain product quality and safety while minimizing waste.
Preventing Pricing Errors in Refrigerated Sections
Maintaining pricing accuracy in refrigerated grocery sections presents unique challenges. Frequent price changes, short product shelf lives, and complex inventory management increase the risk of errors. Electronic shelf labels address these issues by enabling rapid, centralized price updates. For instance, Asda’s trial of electronic shelf labels demonstrated that prices could be updated within 15 seconds, ensuring accuracy and reducing manual labor. Integration with inventory and point-of-sale systems further enhances traceability and compliance. These technologies help grocery retailers avoid costly pricing errors, improve operational efficiency, and support regulatory adherence in cold and frozen sections.
How Electronic Shelf Labels Operate in Cold Environments
Wireless Communication and Real-Time Pricing Updates
Centralized Price Management for Grocery Retail
Grocery retailers require robust solutions to manage pricing across refrigerated and frozen sections. Electronic shelf labels use advanced wireless communication protocols to deliver centralized price management. Modern ESL systems, such as those engineered for cold environments, operate reliably at temperatures as low as -20°C. These systems use frequency hopping and anti-jamming technology, which ensures stable wireless communication even in areas with heavy interference. Bluetooth 5.0 technology further enhances connectivity by offering low power consumption and extended range, making it ideal for large grocery stores with multiple refrigerated aisles.
Note: ESLs with waterproof and frostproof designs maintain continuous operation in cold, humid, and frost-prone environments, ensuring that pricing information remains accurate and visible at all times.
Centralized management allows grocery operators to synchronize price changes instantly across all refrigerated sections. This reduces manual labor and minimizes the risk of errors, supporting compliance and operational efficiency. Electronic shelf labels also support instant refresh and real-time synchronization between online and offline platforms, providing a seamless experience for both staff and customers.
Instantaneous Promotions and Adjustments
Grocery stores often need to implement promotions or adjust prices quickly in response to market trends, inventory levels, or approaching expiration dates. Electronic shelf labels enable instantaneous updates, allowing managers to push new pricing or promotional information to all relevant sections with a single command. This capability ensures that customers always see the most current price, which helps build trust and satisfaction.
- ESLs use dedicated infrastructure, such as RFID readers installed in store ceilings, to communicate wirelessly with shelf labels. These readers receive updates from backend servers and transmit them directly to the ESLs.
- Upon receiving new data, the electronic shelf label immediately refreshes its display and sends a confirmation signal back to the system, verifying successful communication.
This bidirectional communication ensures that every price change or promotion is executed accurately and without delay, even in challenging cold storage environments.
Integration with Store and Inventory Systems
Inventory and Shelf-Life Tracking in Refrigerated Areas
Integration between electronic shelf labels and inventory management systems transforms grocery operations. Middleware solutions connect ESLs with real-time data from IoT sensors and sales transactions. This integration provides visibility into stock levels, product locations, and expiration dates, which is critical for managing perishable goods in refrigerated sections.
Real-time environmental monitoring tracks temperature, humidity, and light exposure, ensuring that products remain in optimal conditions. Predictive analytics estimate remaining shelf life based on current and historical data, helping staff prioritize sales or discounts for items nearing expiration. This approach reduces food waste and maximizes product value.
Tip: Automated inventory tracking and shelf-life management allow grocery retailers to rotate stock efficiently and replenish shelves just in time, reducing spoilage risk.
Automated Data Synchronization for Operational Efficiency
Best practices in grocery retail recommend investing in integrated labeling solutions that connect ESLs with inventory and point-of-sale systems. This integration automates label creation and pricing updates, ensuring real-time price synchronization between shelf labels and checkout systems. Staff no longer need to perform manual price changes, which reduces labor costs and allows them to focus on customer service.
A centralized product database ensures consistent product information across all store systems. Automated updates triggered by inventory changes save time and minimize errors. Advanced barcode and label printing systems compatible with ESLs further streamline operations. Regular audits and clear, consistent label design help maintain accuracy and compliance.
Integration Benefits | Impact on Grocery Operations |
---|---|
Real-time price synchronization | Reduces customer frustration and errors |
Automated inventory tracking | Minimizes food waste and spoilage |
Dynamic pricing capabilities | Supports time-based and demand-based pricing |
Centralized product database | Ensures consistency across all systems |
Data-driven decision-making, enabled by integrated reporting features, helps optimize inventory and pricing strategies. Grocery retailers achieve greater efficiency, improved compliance, and enhanced customer experience by leveraging these advanced electronic solutions.
Key Functionalities of Electronic Price Tags for Refrigerated Sections
Real-Time Pricing and Dynamic Updates
Dynamic Pricing Strategies for Perishables
Grocery retailers face constant challenges in managing perishable inventory. Electronic price tag systems with AI-powered dynamic pricing allow stores to adjust prices in real time based on inventory levels, product freshness, and market demand. These systems optimize pricing at the SKU and store level, eliminating the need for manual intervention. As a result, stores experience faster inventory turnover and reduced overstock. Retailers can set business rules to protect margins and maintain brand positioning while leveraging customer data for targeted promotional campaigns. Studies show that dynamic pricing algorithms can increase revenue by up to 10% and reduce food waste by more than 50% compared to static pricing. This approach also improves customer satisfaction, as shoppers benefit from lower prices on near-expiry goods and more frequent price updates.
Tip: Dynamic pricing not only reduces waste but also enhances competitive positioning by enabling rapid responses to market changes.
- Price adjustments for near-expiry products encourage sales and minimize unsold perishables.
- Gradual price reductions stimulate demand without eroding profits.
- Predictive analytics streamline supply chain management, freeing space for fresh products.
Seasonal and Time-Based Promotions in Grocery
Seasonal and time-based promotional campaigns play a crucial role in grocery retail. Electronic shelf labels enable instant updates for these campaigns, allowing managers to launch or end promotions across all refrigerated sections with a single command. This capability ensures that customers always see accurate, up-to-date prices, which builds trust and encourages repeat visits. Real-time updates also support flash sales and targeted discounts during slow periods, maximizing sales velocity and inventory turnover. By integrating with store systems, ESLs help retailers execute complex promotional strategies without manual errors or delays.
Automated Promotions and Compliance Management
Ensuring Accurate Discounting and Labeling
Accuracy in discounting and labeling remains essential for grocery retailers, especially in refrigerated sections where product turnover is high. ESLs integrate wirelessly with POS and inventory systems, enabling real-time updates of price and product information. This integration reduces manual errors and ensures that shelf prices match checkout prices, minimizing discrepancies. Automated labeling features, such as barcode integration and customizable displays, further improve pricing accuracy and inventory management. Color-coding and visual cues highlight promotional campaigns, making it easier for customers to identify deals.
- Instant price adjustments support dynamic pricing strategies for perishables.
- Automated compliance with pricing regulations reduces the risk of fines and customer distrust.
- Near-instant data transfer and two-way communication empower managers to make timely changes during promotional campaigns.
Meeting Regulatory Standards in Cold Environments
Grocery retailers must comply with strict regulatory standards in refrigerated sections. ESLs designed for cold environments tolerate low temperatures and high humidity, ensuring reliable operation. Automated promotions and real-time updates help stores maintain compliance by providing accurate, up-to-date pricing information. These systems support digital record-keeping, which simplifies audits and inspections. By automating compliance tasks, retailers reduce the risk of regulatory violations and maintain customer trust.
Shelf-Life and Expiry Management with Electronic Shelf Labels
Reducing Food Waste in Refrigerated Retail
Effective shelf monitoring and real-time shelf-life monitoring are critical for reducing food waste in grocery environments. Smart digital labels with energy-efficient e-ink displays operate reliably in refrigerated and freezer conditions. These electronic shelf labels integrate with ERP systems to provide real-time updates on product information, including expiry alerts. Automation enables dynamic label updates, such as changing prices for recalled or expired products. By tracking expiration dates consistently, retailers prevent expired products from being sold and improve the overall customer experience.
- Real-time expiry date tracking allows staff to monitor freshness and prioritize sales of near-expiry items.
- Dynamic pricing and automated discounting help move inventory before spoilage, increasing profits and reducing waste.
- QR code technology on products communicates shelf-life information, encouraging consumer engagement and timely purchases.
Alerting Staff to Expiring Products
ESLs provide visual indicators, such as color-coded LEDs, to alert employees when products approach their expiration dates. This feature enables staff to prioritize restocking and discounting efforts, ensuring that near-expiry items receive attention before spoilage occurs. Real-time data integration with inventory systems helps staff track stock levels and expiration dates efficiently. Automated price changes for expiring products reduce manual labor and errors, freeing employees for other tasks. Data-driven decision-making improves inventory and pricing strategies, minimizing shrinkage and supporting better outcomes for both retailers and customers.
Feature | Benefit |
---|---|
Expiry alerts | Reduces food waste and spoilage |
Automated discounting | Moves inventory before expiration |
Visual indicators (LEDs, colors) | Guides staff to prioritize expiring products |
Real-time data integration | Improves shelf monitoring and efficiency |
Note: Smart digital labels and ESLs support first-in/first-out inventory techniques, helping grocery retailers maintain freshness and maximize margins in refrigerated sections.
Durability and Reliability of Electronic Price Tags in Extreme Conditions
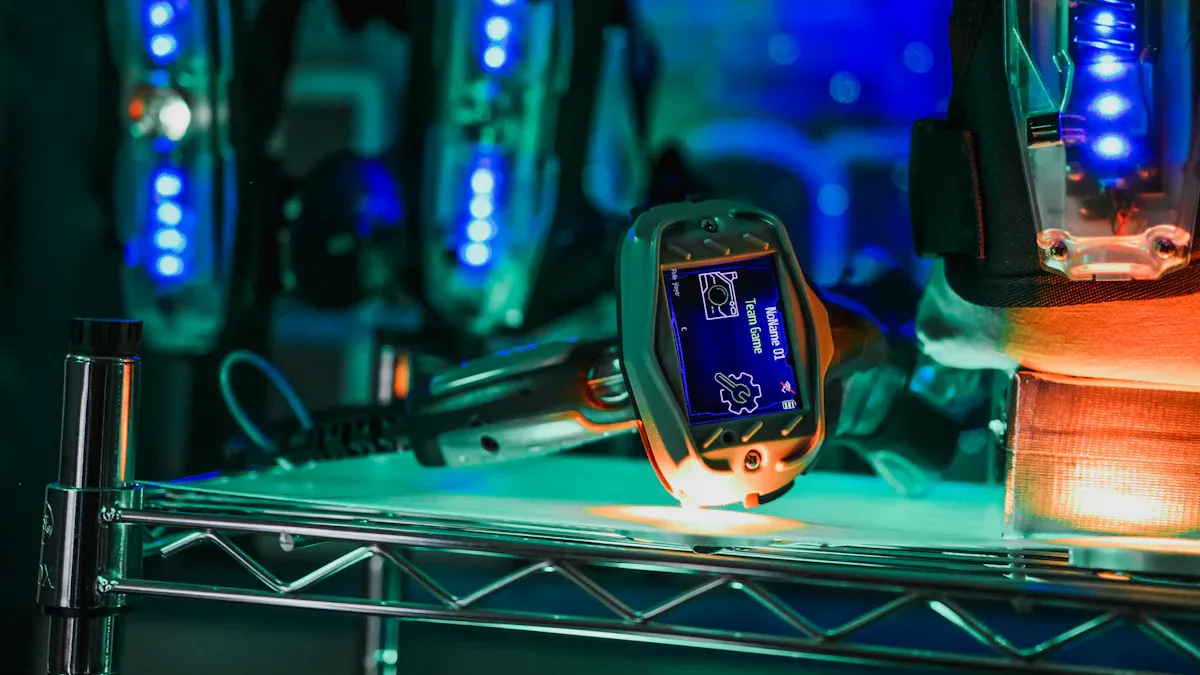
Waterproof and Moisture-Resistant Design
Sealed Casings and Protective Materials for Freezers
Manufacturers design low-temperature esl models like the HS213F and HS266F to withstand the harsh realities of refrigerated and freezer environments. These devices operate efficiently between -25°C and 25°C, using sealed construction that blocks humidity and moisture. Specialized coatings and materials repel water, preventing damage from spills, condensation, or cleaning solutions. The sealed casings also ensure that the esl remains hygienic and easy to clean, tolerating disinfectants without degradation. This robust design extends the lifespan of each tag, reducing the need for frequent replacements and supporting reliable performance in every frozen environment.
- Waterproof shelf labels use advanced seals and coatings to prevent moisture penetration.
- These labels tolerate exposure to liquids, humidity, and cleaning agents.
- The waterproof feature allows flexible placement in produce, dairy, and freezer sections.
Performance in High-Humidity and Frost-Prone Environments
Electronic shelf labels outperform traditional paper tags in high-humidity and frost-prone areas. Paper labels often curl, peel, or lose adhesion when exposed to moisture and temperature swings. In contrast, low-temperature esl solutions maintain clarity and adhesion, even in challenging conditions. The table below highlights the difference in durability and maintenance needs:
Label Type | Durability in High-Humidity/Frost | Maintenance Needs | Lifespan |
---|---|---|---|
Traditional Paper | Prone to adhesive failure, curling, peeling due to humidity and temperature fluctuations | High (frequent reprinting and careful storage) | 1–3 months |
E Ink ESLs (e.g., Datallen Cedar Series) | Waterproof and freeze-resistant down to -20°C, suitable for fresh/frozen sections | Low (battery replacement every 5 years) | 5+ years |
Electronic shelf labels reduce maintenance costs and improve operational efficiency by enabling instant updates and minimizing environmental damage.
Battery Life and Power Efficiency in Cold Temperatures
Longevity and Maintenance in Low-Temperature Settings
Battery performance is crucial for electronic price tags in cold storage. In freezer conditions, typical battery life drops to about 3 years, while refrigerated environments support up to 7 years. At room temperature, batteries can last as long as 10 years. The following chart illustrates this difference:
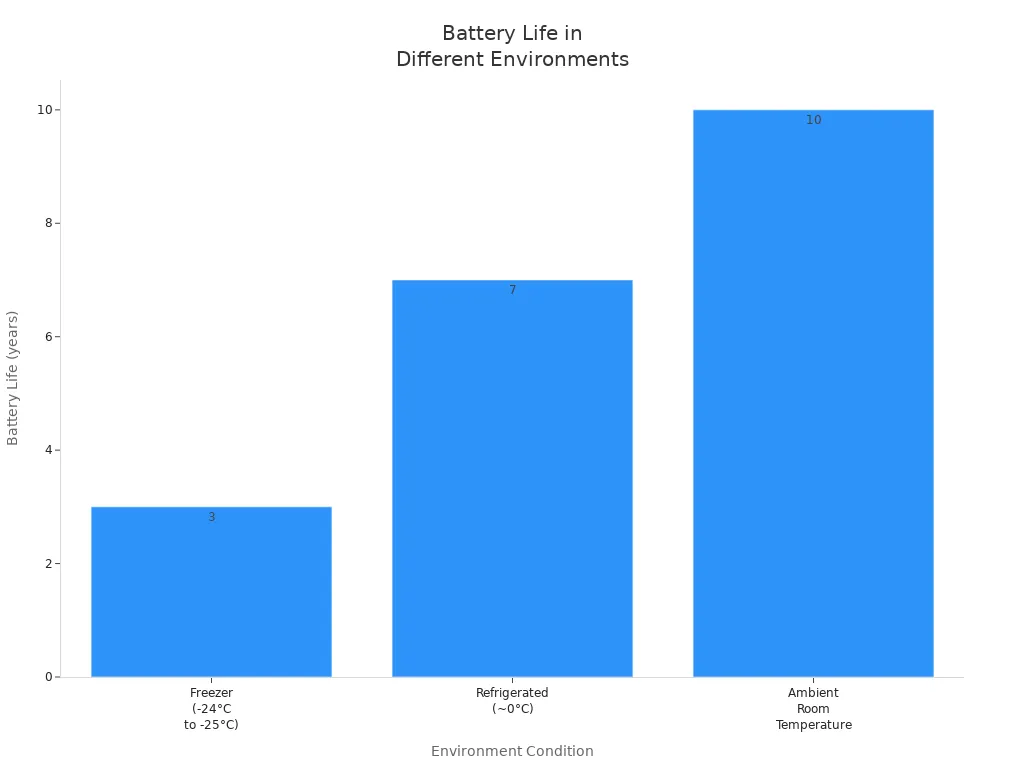
Selecting durable, temperature-resistant esl models ensures reliable operation and reduces the frequency of battery changes, even in sub-zero aisles.
Battery Replacement and Upkeep for Operational Efficiency
Retailers maximize operational efficiency by choosing esl devices with long battery life and protective features such as IP65/68 certification. Regular audits and remote management systems streamline maintenance tasks. Staff can monitor battery status and schedule replacements proactively, minimizing disruptions. Scratch-resistant surfaces and robust construction further reduce the risk of damage during daily operations.
Resistance to Temperature Fluctuations
Consistent Operation in Freezers and Coolers
Low-temperature esl technology ensures consistent performance during frequent temperature changes. These tags function reliably from -25°C to 15°C, maintaining accurate pricing and product information in both coolers and freezers. Durable materials and advanced engineering prevent failures caused by condensation or frost, supporting uninterrupted retail operations.
Testing and Certification Standards for Grocery Retail
Manufacturers subject electronic price tags to rigorous testing for durability and reliability. Devices must meet industry standards for waterproofing, impact resistance, and temperature tolerance. Certifications such as IP65/68 confirm that the tags can withstand wet, cold, and physically demanding environments. These standards guarantee that retailers can trust their monitoring and pricing systems, even in the most challenging refrigerated retail settings.
Real-World Use Cases and Success Stories in Grocery and Beyond
Grocery Store Refrigerated Aisles
Dairy and Deli Sections with Electronic Shelf Labels
Major grocery retailers have adopted electronic shelf labels to streamline operations in dairy and deli aisles. Walmart, for example, began rolling out these systems in over 2,000 stores, including refrigerated sections. This technology enables price changes as often as every ten seconds, which supports the fast-paced nature of fresh food management. Whole Foods, Schnucks, and Amazon Fresh have also implemented these solutions. Employees spend less time walking aisles to update tags and more time restocking or assisting customers. Scannable barcodes on the labels provide shoppers with additional product information, improving the overall experience. A study by leading universities found that after introducing electronic shelf labels, stores saw a slight increase in discounts but no surge in pricing, which reassures customers about fair practices.
Grocery Store | Location | Implementation Details | Benefits & Outcomes | ROI Timeline |
---|---|---|---|---|
Naifeh’s Cash Saver | Covington, Tennessee | Installed digital shelf tags from VusionGroup; handles up to 2,000 weekly price changes | Reduced labor from 50 hours/week to minutes; increased pricing accuracy; color-coded promotions; WIC display | Less than 2 years |
Maurer’s Market IGA | Wisconsin Dells, WI | Installed digital labels for 20,000 SKUs; paid $208,000 | Improved pricing management and accuracy | 1.5 to 2.5 years |
Houchens Food Group | Bowling Green, KY | Testing digital shelf labels in two stores | Expected benefits in pricing efficiency and accuracy | About 3.5 years |
These examples show how electronic shelf labels help grocery stores manage frequent price changes and maintain accuracy in refrigerated aisles.
Fresh Produce and Prepared Foods Pricing
Fresh produce and prepared foods require constant attention to pricing and shelf life. Electronic shelf labels allow grocery staff to update prices instantly for items nearing expiration. This reduces waste and ensures customers always see accurate information. The technology also supports color-coded promotions, making it easier for shoppers to spot deals on fresh items. By automating these updates, stores improve both efficiency and customer satisfaction.
Frozen Food Departments and Electronic Price Tag Applications
Ice Cream and Frozen Meals
Frozen food departments benefit from real-time price changes. Staff can quickly mark down perishable items like ice cream or frozen meals as they approach expiration. This reduces waste and increases sales. Electronic shelf labels also help communicate out-of-stock information, which minimizes customer frustration.
- Real-time price updates support quick markdowns.
- QR codes on labels let customers order out-of-stock items online.
- Dynamic pricing responds to seasonal trends and inventory levels.
Bulk Frozen Goods Management
Managing bulk frozen goods presents unique challenges. Electronic shelf labels provide accurate inventory data, helping staff avoid overstock and stockouts. Stores can launch promotions faster, improving revenue and reducing manual work. Labor cost reductions reach up to 50% for label management, with a return on investment often seen within three years.
Benefit Category | Description | Measurable Impact |
---|---|---|
Labor Cost Reduction | Eliminates manual price changes by enabling instant price updates from a central system. | Up to 50% savings on label management costs; ROI within 1.5 to 3 years. |
Dynamic Pricing | Real-time price updates allow quick markdowns, especially for perishable items like frozen foods. | Increased sales and reduced waste through timely markdowns. |
Inventory Management | Real-time stock data reduces overstock and stockouts. | Improved stock accuracy and reduced lost sales. |
Customer Satisfaction | Accurate, up-to-date pricing and product info enhance shopper experience. | Higher customer loyalty and reduced pricing errors. |
Promotional Agility | Faster and more frequent promotions enabled by ESL technology. | Increased promotional effectiveness and revenue. |
Specialty Retail and Pharmacy Refrigeration Units
Convenience Stores with Refrigerated Displays
Convenience stores use electronic shelf labels to manage pricing in small refrigerated displays. Staff can update prices for beverages, snacks, and fresh food quickly. This flexibility supports frequent promotions and helps stores respond to local demand. Customers benefit from clear, accurate pricing and easy-to-read labels.
Pharmacy Refrigeration Units for Sensitive Products
Pharmacies rely on precise temperature control for sensitive products like vaccines and specialty medications. Electronic shelf labels ensure accurate pricing and product information in these refrigerated units. Staff can monitor inventory and update labels remotely, reducing the risk of errors. This technology supports compliance with strict regulations and improves patient safety.
Note: Across grocery, frozen food, and specialty retail, electronic shelf labels deliver measurable improvements in efficiency, accuracy, and customer experience.
Cold Chain Logistics and Emerging Markets
Temperature-Controlled Warehousing
Temperature-controlled warehousing plays a vital role in the cold chain, especially for perishable goods. Electronic shelf labels (ESLs) have transformed how warehouses manage inventory and pricing in these environments. Warehouses now use digital tags instead of manual paper labels, which often fail in cold, humid conditions. ESLs connect wirelessly to central pricing systems, allowing real-time updates that ensure accuracy and reduce manual labor.
Warehouses benefit from several key features of ESLs:
- Digital tags withstand low temperatures and high humidity, maintaining visibility and performance.
- E-ink displays offer high contrast and long battery life, making them ideal for cold storage.
- Centralized control enables instant price changes and inventory updates, reducing errors and labor costs.
- NFC and QR code integration allows staff and customers to access detailed product information quickly.
- AI-driven dynamic pricing algorithms help optimize stock turnover and minimize waste.
Tip: Warehouses using ESLs report improved operational efficiency and better stock management, which leads to less spoilage and reduced food waste.
The retail sector dominates ESL adoption, with over 83% of revenue share, driven by the need for pricing accuracy and efficiency. In North America, rising labor costs and the push for store automation have accelerated ESL growth. The U.S. leads this trend, while Canada uses ESLs to manage perishables and reduce waste. The Asia-Pacific region also shows rapid adoption, reflecting innovation in emerging markets.
Logistics for Perishable Goods
Efficient logistics for perishable goods depend on accurate, timely information and rapid response to changing conditions. ESLs streamline cold chain logistics by automating price updates and inventory management from distribution centers to store shelves. This automation reduces handling, minimizes spoilage, and supports direct deliveries.
Key advantages of ESLs in perishable goods logistics include:
- Real-time dynamic pricing for products nearing expiration, which helps reduce food waste.
- Centralized inventory control that automates price changes and reduces manual errors.
- Enhanced sustainability by cutting paper usage and supporting ESG goals.
- Synchronization of pricing and inventory across online and offline channels, enabling true omnichannel retailing.
- Features like NFC and QR codes provide transparency and improve traceability throughout the supply chain.
Retailers in emerging markets use ESLs to digitize operations and adapt to fluctuating demand. These technologies enable dynamic pricing strategies, improve customer satisfaction, and support innovation in the global cold chain. As a result, ESLs have become essential tools for managing perishable goods efficiently and sustainably.
Installation, Maintenance, and ROI of Electronic Price Tags
Easy Installation Process for Refrigerated Shelves
Retrofitting Existing Grocery Shelves
Installing electronic price tags on refrigerated shelves follows a clear, step-by-step process. Technicians begin by unboxing and inspecting each electronic shelf label, organizing them by aisle or section. They remove old price tags and adhesive residue, then clean shelf edges with a lint-free cloth to ensure proper mounting. Next, they mount rails or hardware—such as screws, clips, or adhesive strips—onto the shelf edges. For refrigerated shelves, specialized mounts like peg hook brackets or pole-to-ice mounts provide secure attachment. After mounting, technicians attach the electronic shelf labels to the rails or accessories. They connect each label to the store’s wireless network and pair it with management software using tools like NFC controllers. Finally, they verify that each label displays accurate pricing and test real-time updates. Technicians walk the aisles to check for connectivity issues or display errors, making adjustments as needed.
Initial Setup and Staff Training
After installation, staff receive training on the management software and label operation. Training covers how to update prices, monitor label status, and troubleshoot basic issues. Employees learn to use mobile devices or NFC tools for quick pairing and data entry. This training ensures that grocery store operations run smoothly and that staff can handle routine updates or minor issues without delay.
Ongoing Maintenance and Support for Electronic Shelf Labels
Battery Replacement and Upkeep
Ongoing maintenance for electronic shelf labels in refrigerated environments includes regular battery checks and replacements. Highly-trained technicians handle expert installation and maintenance, using original performance parts to extend product life. Condition-based maintenance, enabled by technologies like StoreConnect, predicts failures and improves first-time fix rates. This approach reduces downtime and supports reliable grocery operations.
Software Updates and Troubleshooting in Cold Environments
Software updates keep the system secure and functional. Technical resources and training opportunities help staff manage updates and troubleshoot issues. Refrigeration program management services offer expert project execution and upgrades tailored to refrigerated retail. These services ensure that electronic shelf labels continue to perform well, even in challenging cold environments.
Calculating Return on Investment and Operational Efficiency
Labor Savings and Error Reduction
Retailers calculate return on investment for electronic price tag systems by comparing initial costs—such as labels, installation, software licensing, and maintenance—against labor savings and error reduction. Key cost-saving factors include significant time savings on price updates, especially for stores with frequent changes or promotions. Increased pricing accuracy builds customer trust and reduces checkout discrepancies. The ability to quickly adapt prices for perishable items or respond to market shifts adds further value.
Cost-Saving Factor | Impact on Grocery Store Operations |
---|---|
Time savings on price updates | Frees staff for customer service tasks |
Increased pricing accuracy | Reduces errors and improves trust |
Quick price adaptation | Minimizes waste and maximizes revenue |
Sustainability benefits | Cuts paper and plastic waste |
Enhanced Customer Experience and Compliance
Integration with POS and inventory systems enhances efficiency and accuracy. Electronic price tags support sustainability by reducing paper and plastic waste. Maintenance and upgrades, such as battery replacement or switching to color displays, factor into long-term ROI. Retailers often obtain custom quotes and review case studies from similar stores to estimate ROI effectively. These systems help grocery retailers deliver a better customer experience and maintain compliance with industry standards.
Tip: Regular maintenance and timely upgrades ensure that electronic shelf labels continue to deliver value and support smooth grocery store operations.
Future Trends in Refrigerated Retail and Electronic Shelf Labels
Advancements in Smart Tag Features for Grocery
Enhanced Sensors and Analytics for Pricing Optimization
Smart electronic shelf labels continue to evolve. Manufacturers now equip these tags with advanced sensors that monitor temperature, humidity, and even product movement. These sensors collect real-time data from the refrigerated environment. Retailers use this information to optimize pricing strategies for perishable goods. For example, a sensor can detect when a cooler’s temperature rises above safe levels. The system can then trigger alerts or adjust pricing to move at-risk products quickly.
Analytics platforms process this sensor data to identify trends and patterns. Retailers gain insights into which products sell fastest at certain temperatures or times of day. They can use these insights to set dynamic prices that maximize sales and reduce waste. Data-driven pricing helps stores stay competitive and meet customer expectations.
Tip: Enhanced analytics allow grocery managers to make smarter decisions about promotions and markdowns, especially for items with short shelf lives.
Integration with IoT and AI for Operational Efficiency
The integration of electronic shelf labels with Internet of Things (IoT) devices and artificial intelligence (AI) systems marks a significant trend. IoT connectivity links shelf labels to refrigeration units, inventory systems, and even mobile apps. This network enables automatic updates and remote monitoring. AI algorithms analyze sales data, inventory levels, and environmental conditions. The system can then recommend price changes or reorder products before shelves run empty.
Retailers benefit from fewer manual tasks and faster response times. Automated alerts notify staff about equipment failures or low stock. AI-driven insights help stores predict demand and adjust pricing in real time. This level of automation improves efficiency and reduces operational costs.
Expanding Applications Beyond Food Retail
Healthcare and Laboratory Refrigeration
Electronic shelf labels now find applications in healthcare and laboratory settings. Hospitals and research labs use these tags to monitor sensitive items like vaccines, medications, and biological samples. The labels track temperature and expiration dates, ensuring compliance with strict regulations. Staff receive instant alerts if storage conditions change, which helps protect valuable inventory.
Cold Chain Logistics and New Market Opportunities
Cold chain logistics companies adopt electronic shelf labels to manage inventory in temperature-controlled warehouses and during transport. These tags provide real-time visibility into product location and condition. Logistics managers use this data to prevent spoilage and ensure timely deliveries. Emerging markets also explore electronic shelf labels for pharmaceuticals, specialty foods, and floral products. The technology supports traceability and transparency throughout the supply chain.
Note: As electronic shelf labels become more advanced, industries beyond grocery retail will continue to discover new ways to improve efficiency and safety.
Smart electronic price tags and shelf labels transform refrigerated grocery retail. These solutions deliver real-time pricing, reduce manual errors, and ensure compliance with food safety standards. Retailers experience improved efficiency and greater customer satisfaction.
- Boost operational efficiency
- Maintain regulatory compliance
- Enhance the shopping experience
Tip: Retailers seeking a competitive edge should consider upgrading to smart electronic price tags for reliable, future-ready operations.
FAQ
What makes electronic price tags suitable for refrigerated environments?
Manufacturers design electronic price tags with waterproof casings and moisture-resistant materials. These features protect the tags from condensation, frost, and temperature swings. The tags maintain clear displays and reliable operation in both coolers and freezers.
How do electronic shelf labels update prices in real time?
Electronic shelf labels connect wirelessly to a central management system. Store managers send price changes through software. The labels receive updates instantly, ensuring accurate pricing across all refrigerated sections.
Can electronic price tags help reduce food waste?
Yes. Electronic price tags track product shelf life and expiration dates. The system alerts staff to expiring items and enables dynamic pricing. This approach encourages timely sales and reduces spoilage.
How long do batteries last in cold storage conditions?
Battery life depends on temperature. In freezer environments, batteries typically last about three years. In refrigerated areas, they can last up to seven years. Regular monitoring ensures timely replacements.
Are electronic price tags compliant with food safety regulations?
Electronic price tags support compliance by providing accurate, up-to-date pricing and product information. The system maintains digital records for audits. The tags withstand cold and humid conditions, meeting industry standards for refrigerated retail.
What is the installation process for electronic shelf labels in refrigerated aisles?
Technicians clean shelf edges, mount rails or brackets, and attach the electronic labels. They connect each label to the store’s wireless network and verify display accuracy. Staff receive training on software and label management.
Can stores integrate electronic price tags with inventory systems?
Yes. Electronic price tags integrate with inventory and point-of-sale systems. This integration automates price updates, tracks stock levels, and synchronizes product information. The result is improved efficiency and fewer manual errors.
Do electronic shelf labels require frequent maintenance?
Electronic shelf labels require minimal maintenance. Staff monitor battery status and replace batteries as needed. Software updates and occasional cleaning keep the system running smoothly. Most maintenance tasks can be managed remotely.