In retail, catering, and warehousing, price tags are deceptively simple yet critically impactful tools. While paper tags have long been the “default” solution, electronic shelf labels (ESL) are gaining traction for their dynamic capabilities. This analysis compares the total cost of ownership (TCO) of ESL and paper tags across key dimensions—including initial investment, operational expenses, hidden losses, and long-term benefits—to help businesses determine which option aligns with their financial and operational goals.
1. Initial Investment: One-Time Costs
1.1 Paper Price Tags
Paper tags have minimal upfront expenses but require ongoing purchases:
- Material Costs: A single paper tag costs
0.01–
0.03 (standard coated paper). For a mid-sized supermarket (50,000 tags/year), annual material costs range from500 to
1,500. - Printing/Design: Basic printing (black ink on white paper) costs
0.005–
0.01/tag. Custom designs (logos, colors) or specialty paper (e.g., waterproof) can raise this to0.02–
0.05/tag. - Fixatives: Plastic sleeves, adhesive tape, or staples add
0.002–
0.005/tag, bringing total per-tag initial costs to0.017–
0.085.
Example: A 10,000-tag monthly replacement cycle (120,000 tags/year) with basic materials and design costs ~1,200–
3,600 annually.
1.2 Electronic Shelf Labels (ESL)
ESL requires higher initial investment but eliminates recurring material costs:
- Hardware: E Ink displays (the core component) cost
10–
20/tag (7–10-inch screens for retail). For 10,000 tags, upfront hardware costs range from100,000 to
200,000. - Software/System: Cloud-based management platforms (tag control, remote updates, data sync) cost
2,000–
5,000/month (SaaS) or24,000–
60,000/year. - Installation: Labor for deploying tags (e.g., attaching to shelves) costs
0.10–
0.20/tag, adding1,000–
2,000 for 10,000 tags.
Example: A 10,000-tag deployment with mid-range hardware (15/tag) and SaaS software (
3,000/month) has an initial TCO of 150,000 +
36,000 (12-month software) + 1,500 (installation) = **
187,500**.
Key Takeaway: ESL’s initial cost is 10–15x higher than paper tags for the same number of units, but it avoids recurring material expenses.
2. Operational Costs: Yearly Expenses
2.1 Paper Price Tags
Paper tags incur ongoing labor and error-related costs:
- Labor for Replacement: A store employee replaces ~50 tags/hour. For a supermarket replacing 10,000 tags/month (250 tags/day), daily labor time = 5 hours (250/50). At
15/hour, annual labor costs = 5hrs/day ×
15 × 365 days = $27,375. - Error Losses: Manual errors (misplaced/mismatched tags) cost
50–
200 per incident. A study by the National Retail Federation (NRF) found paper tags cause 15% of customer complaints, averaging100/incident. For 10,000 tags/month, annual errors = 15% × 120,000 = 18,000 incidents. Annual error costs = 18,000 ×
100 = $1,800,000.
Example: Total annual operational costs for paper tags = 27,375 (labor) +
1,800,000 (errors) = $1,827,375.
2.2 Electronic Shelf Labels (ESL)
ESL reduces labor and error costs but requires minimal maintenance:
- Labor Savings: ESL enables remote batch updates (e.g., changing 10,000 tags in 10 minutes). For the same supermarket, labor time for tag updates drops from 5 hours/day to 0.5 hours/day. Annual labor savings = (5 – 0.5)hrs/day ×
15 × 365 = **
23,625**. - Error Reduction: ESL’s automated sync with POS systems cuts errors to <1% of incidents. Using the same 18,000 annual incidents, error costs drop to 1% × 18,000 ×
100 = **
180,000**. - Maintenance: Battery replacement (every 2–3 years) costs
0.50/tag. For 10,000 tags, annual maintenance = 10,000 ×
0.50 / 3 = $1,667. Software updates are included in SaaS fees.
Example: Total annual operational costs for ESL = (27,375 –
23,625) (net labor) + 180,000 (errors) +
1,667 (maintenance) = $175,017.
Key Takeaway: ESL slashes labor costs by 90% and error costs by 90% vs. paper tags, despite higher upfront investment.
3. Long-Term Benefits: Beyond Direct Costs
3.1 Efficiency Gains
ESL frees staff from repetitive tasks, enabling them to focus on high-value work:
- Retail: A Walmart pilot found ESL reduced shelf-tagging time by 80%, allowing employees to dedicate 10+ hours/week to customer service, boosting sales by 5% (
1.2M/year for a
24M store). - Warehousing: Amazon reported ESL improved picking accuracy by 30%, reducing returns and customer complaints by $500,000/year for a 1M sq ft facility.
3.2 Revenue Uplift
Dynamic pricing and real-time updates drive sales:
- Promotions: ESL enables “flash sales” or “end-of-day discounts” to be deployed in minutes. A Starbucks case study showed ESL increased promotional conversion rates by 25%, adding $3M/year in revenue for 3,000 stores.
- Inventory Accuracy: ESL syncs with ERP systems, reducing overstock/understock losses by 40%. A global electronics retailer saved $800,000/year in inventory carrying costs.
3.3 Sustainability
ESL eliminates paper waste, aligning with ESG goals:
- A mid-sized supermarket using 120,000 paper tags/year reduces paper consumption by 120 reams/year (equivalent to 6 trees saved).
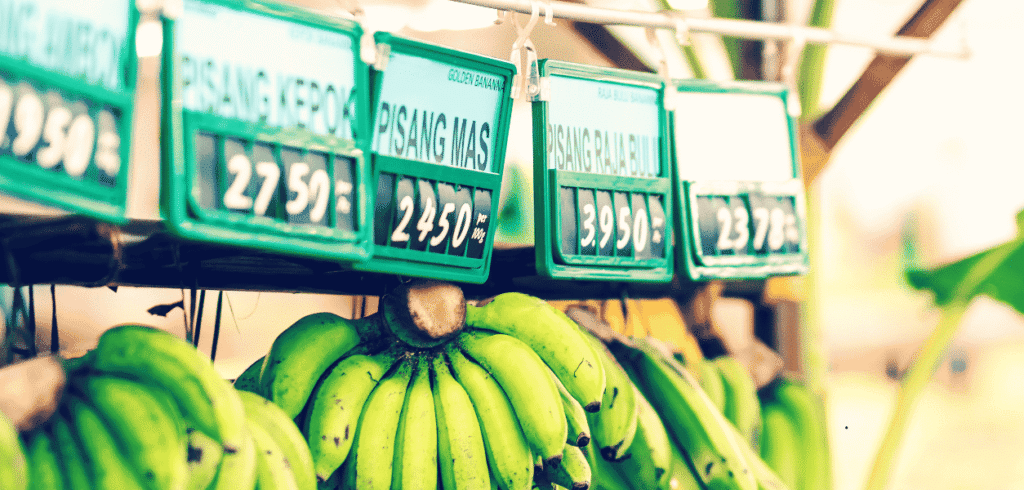
4. Total Cost of Ownership (TCO) Over 5 Years
To compare long-term viability, we calculate TCO for both options over 5 years (assuming 10,000 tags/year):
Cost Category | Paper Tags (5-Year TCO) | ESL (5-Year TCO) |
---|---|---|
Initial Investment | 6,000– 30,000 (materials) | $187,500 (hardware + software) |
Annual Operational Costs | 1,827,375/year × 5 = 9,136,875 | 175,017/year × 5 = 875,085 |
Hidden Losses (Errors/Stock) | 1,800,000/year × 5 = 9,000,000 | 180,000/year × 5 = 900,000 |
Total TCO | $18,163,875 | $1,962,585 |
Note: ESL’s TCO is dramatically lower due to reduced errors, labor, and stock losses.
5. When Does ESL Make Financial Sense?
ESL delivers ROI when:
- Tag Replacement Frequency: High (e.g., supermarkets with daily promotions, seasonal stores).
- Error Costs: Significant (e.g., luxury goods, high-ticket items where mispricing leads to large refunds).
- Labor Costs: Elevated (e.g., urban retailers with high wages).
- Scalability Needs: Multi-location businesses (ESL centralizes tag management across stores).
For small businesses with low replacement frequency (e.g., a corner café changing tags weekly), paper tags may remain cost-effective in the short term.
Conclusion
While ESL requires a higher initial investment, its long-term TCO is 5–10x lower than paper tags due to reduced labor, error, and stock losses, plus efficiency and revenue gains. For enterprises with annual revenues exceeding $5M or high tag replacement volumes, ESL is not just a “cost saver”—it’s a strategic tool to drive profitability, agility, and customer trust.