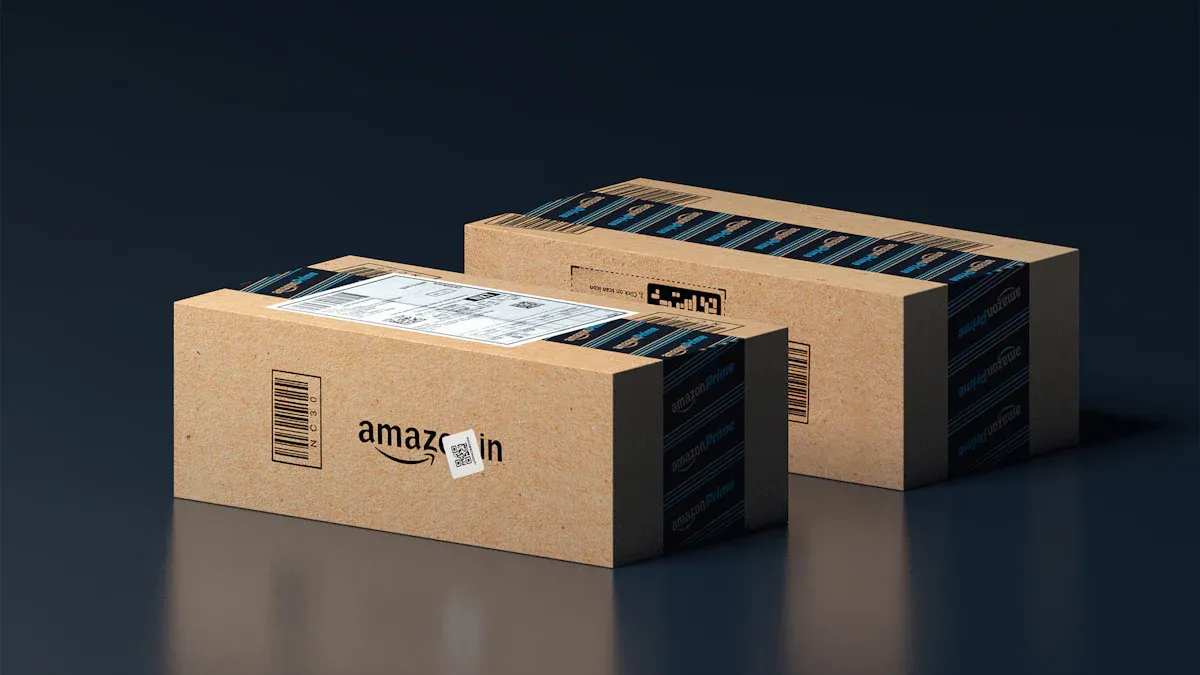
Amazon logistics depends on electronic tags to achieve real-time visibility of every package. These electronic tags include technologies such as Electronic Shelf Labels, ESL Gateway AP, and ESL Price Tag. By leveraging RFID and Esl Retail solutions, Amazon logistics can instantly track each item at every stage. Real-time monitoring supports accurate, secure, and timely deliveries. This robust logistics system improves efficiency and reduces errors in the supply chain.
Electronic Tags in Amazon Logistics
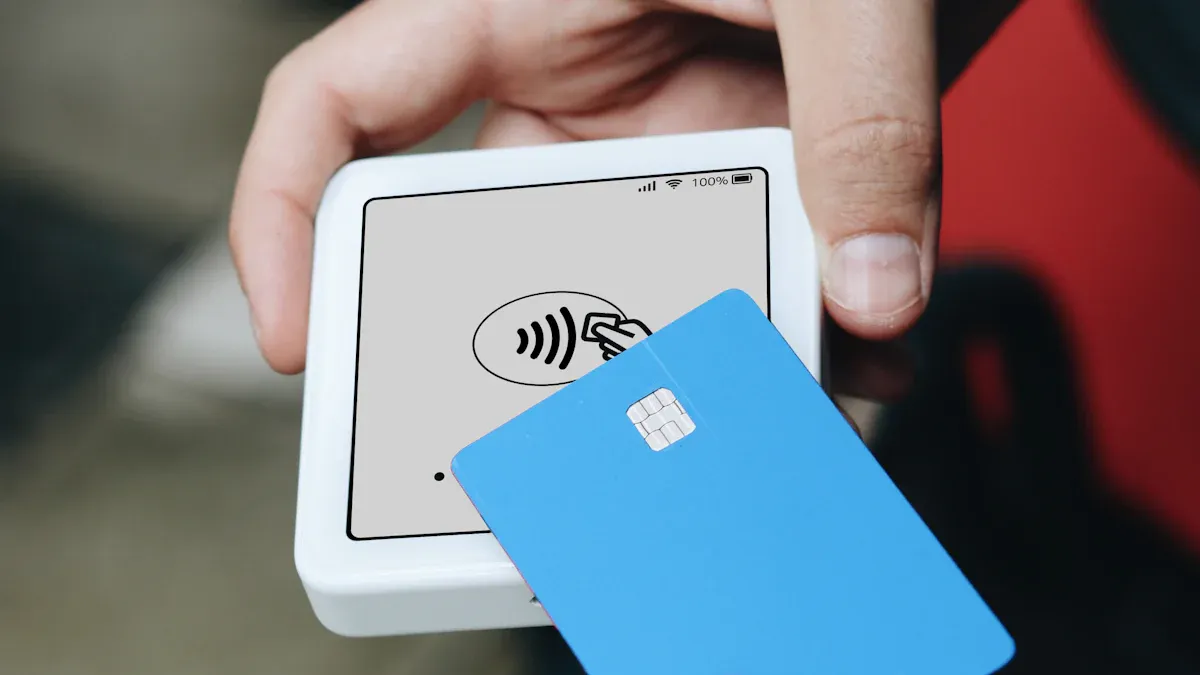
What Are Electronic Tags?
Electronic tags serve as the backbone of asset tracking and real-time tracking in Amazon logistics. These tags include both barcodes and RFID tags, each playing a unique role in the logistics network. Amazon applies tags to every package, pallet, and container, ensuring that each item receives a unique digital identity. This approach enables precise tracking and efficient management of inventory across vast fulfillment centers.
RFID Technology Explained
RFID technology uses radio waves to transmit data between RFID tags and readers. Each RFID tag contains an Electronic Product Code (EPC), which assigns a unique identity to every item. In Amazon logistics, RFID tags enable non-contact, bulk identification of goods. Workers can scan multiple items at once, even if the tags are not visible. This process speeds up warehousing, sorting, and asset tracking, while reducing manual errors. RFID technology also supports real-time inventory checks and accurate item location within large warehouses. By associating EPCs with parcel information, Amazon achieves end-to-end visibility from warehouse to consumer.
Barcodes vs. RFID Tags
Barcodes and RFID tags both support tracking, but they function differently. Amazon uses the sp00 barcode label to uniquely identify each shipping package. This label contains information such as package contents, customer address, and delivery date. The sp00 label integrates with automated systems like the SLAM process, streamlining outbound order fulfillment and adding a security layer by restricting package access to authorized personnel.
Component of LPN Barcode | Description |
---|---|
First 2 Digits | Identify the specific fulfillment center location |
Next 2 Digits | Represent the year the inventory/pallet entered the fulfillment center |
Following 2 Digits | Julian date indicating the calendar date of arrival at the warehouse |
Final 4 Digits | Unique serial number for each barcode printed that day at the fulfillment center |
While barcodes require line-of-sight scanning, RFID tags can be read at distances up to 10 meters and do not need direct visibility. RFID tags also withstand damage better than barcodes, making them ideal for large-scale logistics and asset tracking.
Why Amazon Uses Electronic Tags
Real-Time Tracking Advantages
Amazon logistics relies on RFID tags to deliver real-time tracking and asset tracking at every stage. RFID tags enable item-level identification without manual scanning, allowing multiple items to be tracked simultaneously. This capability improves speed and accuracy in tracking packages and inventory. Real-time tracking provides instant inventory visibility, supporting better inventory management and sales analytics. RFID tags also enhance loss prevention by tracking items throughout the supply chain.
Enhancing Efficiency and Accuracy
RFID technology increases efficiency by automating data collection and reducing manual intervention. RFID tags transmit data wirelessly, enabling real-time updates and minimizing errors. Integration with enterprise systems ensures seamless data flow, boosting operational efficiency across Amazon’s supply chain. RFID tags also simplify returns processing, as returned goods can be quickly identified and processed. By leveraging RFID tags, Amazon logistics optimizes demand forecasting, inventory management, and route planning, resulting in higher efficiency and lower costs.
Step-by-Step: Real-Time Tracking of Packages

Tagging at the Source
Attaching RFID Tags to Packages
Amazon begins the asset tracking process at the source by attaching RFID tags to every package. Workers apply these tags during the initial packaging phase, ensuring that each item receives a unique identifier. The RFID tags contain microchips and antennas that store and transmit data wirelessly. This step establishes the foundation for real-time tracking and inventory identification throughout the logistics network.
The use of RFID tags at this stage allows Amazon to automate asset tracking from the very beginning. Each tag links directly to the package’s information, enabling seamless integration with downstream tracking systems. By standardizing the tagging process, Amazon ensures consistency and accuracy in its warehouse operations.
Encoding and Registering Package Data
After attaching the RFID tags, Amazon encodes each tag with essential package data. This process involves writing information such as product type, destination, and order number onto the tag’s memory. Specialized encoding stations handle this task, ensuring that every tag contains accurate and up-to-date details.
Once encoded, the tags are registered in Amazon’s inventory management system. This registration step connects the physical package to its digital record, enabling real-time updates and asset tracking as the package moves through the supply chain. The system supports bulk encoding, allowing multiple tags to be processed simultaneously, which increases efficiency and reduces manual errors.
Tracking in Amazon Warehouses
Automated Scanning Systems
Inside Amazon warehouses, automated scanning systems play a critical role in tracking packages. RFID readers, developed in collaboration with technology partners, scan the RFID tags attached to products. These readers use advanced antenna arrays to capture tag data without requiring line-of-sight. The system can identify hundreds of tags at once, even in environments with many moving items.
The RFID readers transmit collected data to backend systems hosted on AWS cloud software. This infrastructure supports real-time tracking, asset tracking, and inventory management by providing continuous visibility into package locations. Machine learning algorithms analyze the tag reads, distinguishing between items entering or leaving specific areas. This approach streamlines warehouse operations and enhances the accuracy of inventory identification.
Tip: Automated scanning reduces manual labor and speeds up warehouse processes, making real-time tracking more reliable.
Inventory Management Integration
Amazon integrates RFID tracking with its inventory management system to maintain precise control over stock levels. The system uses RFID tags, readers, antennas, middleware, and software to create a seamless flow of information. The table below summarizes the key components and their functions:
Component | Function |
---|---|
RFID Tags | Store detailed product information and enable wireless identification and tracking |
RFID Readers | Collect data wirelessly from RFID tags to update inventory status in real-time |
Antennas | Enhance signal range of RFID readers for effective coverage across large warehouse areas |
Middleware | Processes RFID data and integrates it into Amazon’s existing inventory management software |
Software System | Analyzes and manages inventory data, triggers automated replenishment, and prevents stockouts |
This integrated system enables real-time updates and asset tracking without manual intervention. Middleware processes the RFID data and feeds it into the inventory management software, which analyzes the information to optimize inventory levels and trigger automated replenishment. The use of UHF RFID technology supports long-range tracking, making it suitable for Amazon’s large-scale warehouse operations.
Amazon also leverages artificial intelligence to analyze real-time inventory data. This integration helps predict purchasing patterns, maintain optimal inventory levels, and personalize customer recommendations. The result is a highly efficient inventory management system that reduces errors and improves customer satisfaction.
Monitoring During Transportation
Real-Time Updates in Transit
Once packages leave the warehouse, Amazon continues asset tracking through transportation tracking systems. RFID tags remain active, allowing RFID readers at various checkpoints to scan and update package status. These real-time updates provide continuous visibility as packages move through distribution centers and transit hubs.
The system records each scan and transmits the data to Amazon’s central inventory management system. This process ensures that every package’s location is known at all times, reducing the risk of lost or misplaced items. Real-time tracking during transit supports proactive problem-solving and enhances delivery reliability.
Delivery Vehicle Tracking
Amazon employs advanced transportation tracking solutions to monitor delivery vehicles and the packages they carry. RFID readers installed in delivery vehicles scan the tags on packages, updating their status as they move toward their final destination. GPS technology works alongside RFID systems to provide precise location data for each vehicle.
This dual approach enables Amazon to track both the vehicle and the individual packages in real time. The system generates automated alerts if a package deviates from its expected route or encounters delays. By combining RFID tags with GPS-based transportation tracking, Amazon ensures secure, efficient, and transparent deliveries.
Note: Real-time tracking and transportation tracking not only improve delivery speed but also enhance security by preventing theft and unauthorized access.
Final Delivery and Confirmation
Last-Mile Real-Time Tracking
The last mile represents the final and most critical phase in Amazon’s logistics chain. During this stage, packages move from local distribution centers to customers’ doorsteps. Amazon deploys advanced tracking technologies to maintain visibility and control throughout this process. Each delivery vehicle carries RFID readers that continuously scan packages as they travel their routes. These readers communicate with Amazon’s central systems, updating package status in real-time.
Drivers use handheld devices that display up-to-date delivery information. These devices receive data from both GPS and RFID systems. The combination of these technologies allows Amazon to monitor the precise location of every package during the last mile. If a package encounters a delay or deviates from its planned route, the system generates an alert for immediate investigation.
Note: Last-mile tracking helps Amazon reduce lost packages and ensures that customers receive accurate delivery estimates.
Amazon’s real-time tracking infrastructure supports dynamic route adjustments. If traffic conditions change or a delivery address requires modification, the system updates the driver’s route instantly. This flexibility improves delivery speed and reliability.
Delivery Verification Process
Upon arrival at the delivery location, Amazon implements a robust verification process to confirm successful handoff. The driver scans the package’s RFID tag one final time using a handheld device. This scan records the exact time and GPS coordinates of the delivery. The system then updates the package status in Amazon’s database, marking it as delivered.
Amazon employs several methods to verify delivery:
- Photo Confirmation: The driver captures a photo of the package at the drop-off point. This image provides visual proof of delivery.
- Electronic Signature: For high-value items, the recipient may sign electronically on the driver’s device.
- Automated Notifications: The system sends a real-time notification to the customer, confirming that the package has arrived.
The table below summarizes the key steps in Amazon’s delivery verification process:
Step | Action Performed | Purpose |
---|---|---|
RFID Tag Scan | Driver scans package at delivery point | Confirms package identity |
GPS Timestamp | Device records location and time | Verifies delivery accuracy |
Photo or Signature | Captures proof of delivery | Provides evidence for records |
Customer Notification | Sends update to customer | Confirms delivery completion |
Amazon’s verification process reduces the risk of theft and disputes. The company maintains a digital record for every delivery, which supports customer service and security investigations if needed.
Tip: Customers can track their packages in real-time and receive instant updates, which increases transparency and trust in the delivery process.
The Technology Powering Amazon Logistics
How RFID Works in Practice
RFID Tag Components and Function
Amazon’s logistics network relies on a sophisticated system of RFID tags to track every package. Each tag contains a microchip and antenna, which store and transmit unique identification data. These tags attach to products, pallets, and containers, enabling bulk identification as items arrive at operations centers. The RFID tags allow Amazon to scan multiple items at once, even without direct line-of-sight, which speeds up warehousing and sorting. This process reduces manual scanning errors and increases efficiency. The unique identifiers on each tag also help combat counterfeiting and secure brand integrity.
RFID Readers and Network Integration
RFID readers play a crucial role in Amazon’s logistics operations. These devices, installed throughout warehouses and on delivery vehicles, capture data from RFID tags using radio waves. The readers work with antennas to extend their range, making them suitable for large-scale environments. Amazon’s network integrates RFID readers with middleware and software platforms, creating a seamless flow of information. Real-time updates from RFID readers feed directly into the inventory management system, providing continuous visibility and supporting automated replenishment. This integration ensures that inventory counts remain accurate and up-to-date, reducing discrepancies and human error.
Amazon’s use of UHF RFID technology enables long-range tracking, which enhances efficiency and reduces manual labor across vast fulfillment centers.
Integration with AI and Software
Machine Learning for Tracking Optimization
Amazon combines RFID data with artificial intelligence to optimize tracking and logistics. AI-powered robots and computer vision systems work alongside RFID readers to locate and fulfill orders in real time. Machine learning algorithms analyze data from RFID tags to predict demand, optimize delivery routes, and personalize customer communications. This integration allows Amazon to automate many warehouse operations, reducing manual labor and improving efficiency.
Data Analytics and Inventory Control
The inventory management system at Amazon leverages data analytics to maintain precise control over stock levels. RFID tags simplify physical inventory tracking, while AI analyzes this data to forecast demand and prevent stockouts. Cloud platforms process RFID data and AI algorithms to provide real-time updates on inventory and supply chain status. This approach supports efficient route planning and ensures that customers receive timely deliveries.
Role of IoT in Real-Time Tracking
Connected Devices in the Logistics Network
Amazon’s logistics network uses the Internet of Things (IoT) to connect all components, from RFID tags to wearable devices. IoT devices, such as smartwatches and smartphones, enable seamless tracking and reduce manual labor in inventory selection. Warehouse managers use these connected devices to monitor inventory and equipment, improving asset utilization and customer service.
Automated Alerts and Updates
IoT technology enhances real-time tracking by providing automated alerts and updates throughout the supply chain. With 5G connectivity and cloud computing, Amazon extracts detailed real-time data, including location and shipment conditions. This information supports predictive maintenance, shipment monitoring, and timely delivery notifications, further increasing efficiency and transparency for both Amazon and its customers.
Benefits of Real-Time Tracking for Amazon and Customers
Improved Accuracy and Speed
Reducing Lost or Misplaced Packages
Amazon logistics has transformed package traceability by implementing real-time tracking systems. Each package receives a unique tracking ID, which workers scan at every stage of the delivery route. Customers can monitor their packages live, especially on delivery day, using Amazon Map Tracking. This feature displays the package’s location as the driver approaches, allowing customers to prepare for receipt or specify a safe drop-off spot. This proactive visibility reduces the risk of lost or misplaced packages. Amazon logistics also maintains constant communication with customers, quickly resolving delivery issues and further minimizing shrinkage.
Faster Order Fulfillment
Amazon logistics leverages real-time tracking and robotics to accelerate order processing. The company improved delivery promise accuracy by 15-20% and achieved over 95% on-time delivery rates for Prime-eligible products. Over three years, Amazon reduced average order processing time by 40% and decreased picking errors by 75%. Optimized packaging now moves 30% faster through fulfillment centers. Sellers who use demand forecasting and inventory placement aligned with real-time data see a 20-30% reduction in storage fees while maintaining 99%+ in-stock rates during peak seasons. Route optimization algorithms process over a billion data points daily, enabling dynamic route adjustments and directly improving delivery accuracy.
📦 Tip: Real-time tracking and asset tracking not only speed up fulfillment but also enhance inventory accuracy and shrinkage prevention.
Greater Transparency and Security
Real-Time Tracking for Customers
Amazon logistics provides customers with real-time tracking, which increases supply chain transparency and trust. The Amazon Transparency Program allows brands to monitor products throughout the supply chain, from manufacturing to delivery. Customers can scan unique Transparency codes to verify authenticity and access detailed product background information. This traceability ensures that customers receive genuine items and understand the journey of their packages.
Preventing Theft and Fraud
By registering products with unique codes, Amazon logistics ensures that customers receive authentic goods, not counterfeits or stolen items. Real-time tracking from supplier to customer offers detailed insights into product provenance and supply chain processes. This transparency enhances customer confidence and loyalty. The system also reduces shrinkage by providing clear visibility into product sourcing and delivery, alongside improved security measures.
Streamlined Inventory and Logistics
Automated Stock Management
Amazon logistics uses real-time inventory tracking across multiple marketplaces, enabling instant stock level monitoring. Automated restock alerts notify managers when inventory reaches thresholds, preventing stockouts. Advanced demand forecasting analyzes sales trends to avoid overstocking and shortages. Automated reordering generates purchase orders based on real-time data, maintaining optimal stock and reducing shrinkage.
Efficient Route Planning
Amazon’s inventory management system integrates with robotics and warehouse management systems to streamline operations. Real-time data supports efficient picking, packing, and shipping, improving delivery speed and customer satisfaction. Route optimization algorithms enable dynamic adjustments based on traffic, weather, and customer preferences. This operational efficiency reduces shrinkage and ensures reliable deliveries.
🚚 Note: End-to-end traceability and supply chain transparency help Amazon logistics maintain high inventory accuracy, minimize shrinkage, and deliver a seamless customer experience.
Challenges and Concerns in Amazon Logistics
Privacy and Data Security
Protecting Customer Information
Amazon manages vast amounts of sensitive data throughout its logistics operations. The company must protect customer information at every stage, from order placement to final delivery. Electronic tags and tracking systems collect detailed data, including package location and delivery status. Amazon implements strict security protocols to safeguard this information and prevent unauthorized access. The company uses encryption and access controls to ensure that only authorized personnel can view or modify sensitive records. These measures help reduce the risk of data breaches and protect customer trust.
Addressing Privacy Concerns
Privacy concerns extend beyond customer data. Amazon’s use of electronic wristbands to monitor warehouse workers highlights the complexity of balancing efficiency with privacy. These wristbands track every movement, including minor actions such as scratching or taking breaks. The devices can even vibrate to prompt workers if they slow down. Many consider this level of surveillance invasive. It raises questions about workplace privacy and the extent of behavioral monitoring in logistics environments. Amazon must address these concerns by maintaining transparency and ensuring that monitoring practices comply with privacy regulations.
Cost and Implementation Barriers
Investment in RFID Technology
Implementing RFID technology at Amazon’s scale involves significant cost. The company must invest in expert programmers and engineers to design complex systems. Extensive prototype testing and ongoing debugging add to the financial burden. Amazon also allocates resources for employee training and empowerment, which increases overall cost. The need for continuous monitoring and improvement requires ongoing investment. Aligning RFID systems with global business needs and adapting to market changes further complicate the cost structure.
Scaling Across the Logistics Network
Scaling RFID technology across Amazon’s logistics network presents additional challenges. Organizational resistance to change can slow implementation. Employees must adapt to new processes, which demands comprehensive training programs. Managing organizational culture becomes critical to successful adoption. Amazon must allocate resources for change management and continuous improvement. The company faces the ongoing cost of maintaining and upgrading systems to keep pace with evolving logistics demands.
- Key cost and implementation barriers include:
- System design complexity
- Extensive testing and debugging
- Employee training and empowerment
- Resistance to change and culture management
- Continuous monitoring and improvement
- Adapting to global business needs
💡 Tip: Addressing these barriers helps Amazon control shrinkage and maintain operational efficiency.
Technical Limitations
Tag Readability and Environmental Factors
Technical limitations can impact the effectiveness of electronic tags. Amazon enforces strict labeling and barcoding requirements for all products entering its logistics network. Vendors must apply barcode labels that meet Amazon’s specifications to ensure readability. Amazon offers labeling services for sellers who need assistance. This barcode-driven approach supports product traceability and helps control shrinkage by maintaining operational efficiency.
Amazon also employs advanced AI vision-language models in fulfillment centers. These models analyze product images to verify label information, even when labels are partially obscured or damaged. If a customer reports an issue, the AI system cross-references feedback with fulfillment center images to confirm product details. Imaging tunnels detect defects such as wrong color or expired items, enabling real-time quality control and reducing shrinkage.
Handling Tag Failures
RFID technology faces challenges such as high cost and readability issues in certain environments. Amazon addresses these limitations by focusing on logistics synchronization. The company aligns warehouse operations, transportation, and delivery schedules to optimize efficiency. AI-driven quality control and precise process coordination help overcome technical barriers. This approach minimizes shrinkage and ensures reliable package tracking, even when tag failures occur.
The Future of Electronic Tags and Real-Time Tracking at Amazon
Advancements in RFID and Tracking Technology
Smarter, Smaller, and Cheaper Tags
Amazon continues to invest in the evolution of rfid tags. The next generation of tags will become smaller, smarter, and more affordable. Miniaturized rfid tags will attach to a wider range of products, including small electronics and reusable packaging. These advanced tags will store more data and support enhanced security features, such as real-time alerts for unauthorized access. As rfid tags become less expensive, Amazon can deploy them across more items, improving traceability and reducing manual labor.
- Miniaturized rfid tags will enable tracking of individual items, not just pallets or boxes.
- Enhanced tags will support real-time data analysis, allowing Amazon to identify issues instantly.
- Lower costs will make it possible to tag even low-value products, increasing overall supply chain transparency.
These improvements will drive greater efficiency and operational control. Automation will reduce labor costs and minimize losses from misplaced goods.
Integration with IoT and Automation
Amazon integrates rfid tags with the Internet of Things (IoT) to create a connected logistics network. IoT devices, such as sensors and smart readers, communicate with rfid tags to monitor inventory and vehicle conditions in real time. This integration allows Amazon to optimize fleet management and automate inventory checks. Autonomous robots equipped with rfid readers will conduct inventory audits, reducing the need for manual counts.
- IoT-connected rfid tags provide instant updates on package location and condition.
- Automated replenishment systems use rfid data to maintain optimal stock levels.
- Real-time monitoring supports route optimization and faster deliveries.
By combining rfid tags with IoT and automation, Amazon enhances supply chain transparency and reduces costs and delays.
Expanding Applications in Amazon Logistics
Tracking Returns and Reusable Packaging
Amazon expands the use of rfid tags to manage returns and reusable packaging. These tags track products throughout their lifecycle, supporting circular economy initiatives. When customers return items, rfid tags provide instant traceability, allowing Amazon to process returns quickly and efficiently. The company also uses tags to monitor reusable containers, ensuring they return to the correct location for cleaning and reuse.
- Rfid tags help Amazon identify returned products and verify their authenticity.
- Lifecycle tracking supports refurbishment and recycling, reducing waste.
- Automated systems streamline the handling of reusable packaging, improving sustainability.
This approach increases traceability and supports Amazon’s commitment to environmental responsibility.
Enhancing Supply Chain Visibility
Amazon leverages rfid tags to improve supply chain visibility at every stage. Real-time data from tags enables the company to monitor inventory, shipments, and vehicle locations with precision. Advanced analytics provide insights into bottlenecks and inefficiencies, allowing Amazon to make data-driven decisions.
- Rfid tags enable end-to-end traceability, from supplier to customer.
- Enhanced visibility reduces errors and improves delivery performance.
- Data-driven insights support continuous improvement in logistics operations.
📈 Tip: Companies that invest in rfid tags and advanced tracking systems gain a competitive edge through improved traceability and supply chain transparency.
Electronic tags and real-time tracking form the backbone of Amazon’s logistics network. These technologies deliver precise, efficient, and secure package delivery. Amazon gains operational speed and accuracy, while customers benefit from transparency and reliability.
As technology advances, Amazon stands ready to adopt smarter tracking solutions. The company continues to address challenges, driving innovation in logistics for the future.
FAQ
How does Amazon use electronic tags to track packages?
Amazon attaches electronic tags, such as RFID tags and barcodes, to every package. These tags store unique data. Automated systems scan the tags at each stage, updating the package’s status in real time.
What is the difference between RFID tags and barcodes in Amazon logistics?
RFID tags transmit data wirelessly and do not require line-of-sight scanning. Barcodes need direct scanning. RFID tags allow Amazon to track multiple packages at once, while barcodes support individual identification.
How does real-time tracking improve Amazon’s delivery process?
Real-time tracking provides instant updates on package location. This system reduces errors and speeds up order fulfillment. Customers receive accurate delivery estimates and notifications, which increases transparency and trust.
Does Amazon use electronic tags for checkout-free technology?
Amazon uses electronic tags and sensors to enable checkout-free technology in select stores. These systems, often called just walk out technology, allow customers to shop and leave without traditional checkout lines.
How does Amazon ensure data security with electronic tags?
Amazon uses encryption and strict access controls to protect data collected from electronic tags. Only authorized personnel can access sensitive information. These measures help maintain customer privacy and data integrity.
Can electronic tags support frictionless shopping experience?
Electronic tags play a key role in creating a frictionless shopping experience. They enable automated tracking, inventory management, and checkout-free shopping, reducing wait times and manual processes for customers.
What happens if an RFID tag fails during delivery?
If an RFID tag fails, Amazon’s logistics system relies on backup methods, such as barcode scanning and manual checks. This redundancy ensures that packages remain traceable throughout the delivery process.
For more details on Amazon’s logistics technology, visit the official Amazon logistics resources.