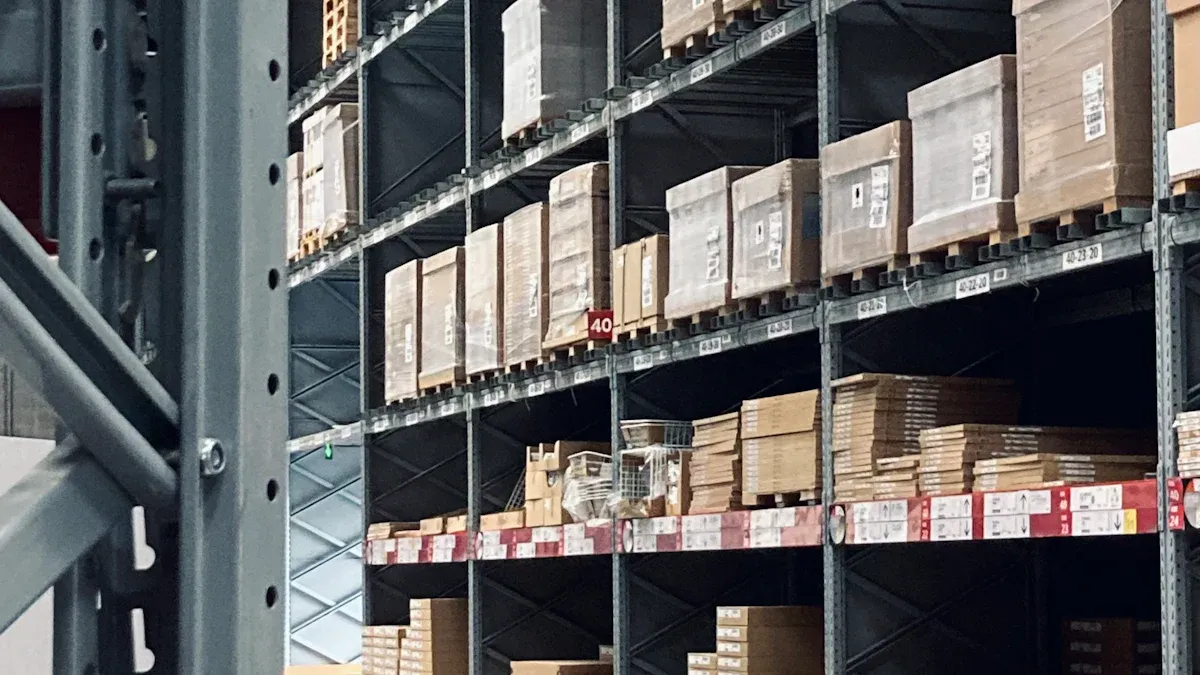
Selecting the right shelf labeling system for your business transforms how you manage products and streamline daily operations. When you match your shelf labeling and materials to your environment, you boost efficiency and inventory accuracy. Many businesses see order filling accuracy climb to 99.9% and back-order rates drop below 0.20% after upgrading their labeling systems. Electronic Shelf Labels, including solutions like ESL Price Tag and ESL Gateway AP, help Esl Retail operations adapt quickly. Clear shelf labeling supports faster decision-making and long-term growth.
Assessing Inventory and Storage for Shelf Labeling
When you choose a shelf labeling system, you must first understand your inventory and storage needs. This assessment helps you select labels that work best for your warehouse environment and daily operations.
Identifying Inventory Types and Volumes
Product Variety and Turnover Rates
You should start by analyzing the variety of products in your warehouse. High product variety often requires a flexible labeling system. If your inventory turnover rate is high, you need labels that can handle frequent changes. In a busy warehouse, products move quickly from one storage location to another. You must ensure your labeling system can keep up with these changes without causing confusion or delays.
Item Size, Shape, and Packaging
Consider the size, shape, and packaging of each item. Large or oddly shaped items may need bigger labels or special placement on the storage shelf. Small items might require compact labels that still offer clear information. You should match the label size to the available space at each storage location. This step prevents misplacement and improves accuracy during picking and restocking.
Evaluating Storage Environments
Temperature, Humidity, and Lighting
Your warehouse environment affects label durability. Extreme temperatures or high humidity can damage labels and make them unreadable. Poor lighting in some storage areas can also reduce label visibility. You should select materials that withstand your warehouse conditions. For example, synthetic labels often perform better in cold storage or high-humidity locations.
Exposure to Chemicals, Dust, or Moisture
Some warehouse zones expose labels to chemicals, dust, or moisture. In these areas, you need labels that resist smudging and peeling. Durable materials and strong adhesives help labels stay in place on every storage location. You should regularly inspect labels in these challenging environments to maintain clear identification.
Understanding Operational Workflows
Frequency of Inventory Changes
If your warehouse experiences frequent inventory changes, you need a labeling system that adapts quickly. Removable or magnetic labels work well in dynamic storage locations. You can update these labels without damaging shelves or racks. This flexibility supports efficient warehouse operations.
Staff Access and Navigation Patterns
You should observe how staff move through the warehouse. Easy-to-read labels at every storage location help workers find products faster. Place labels at eye level or along common pathways to improve visibility. When you align your labeling system with staff navigation patterns, you reduce search time and boost productivity.
Tip: Regularly review your warehouse layout and storage practices. Adjust your labeling system as your inventory and workflows evolve.
Exploring Shelf Labeling System Options
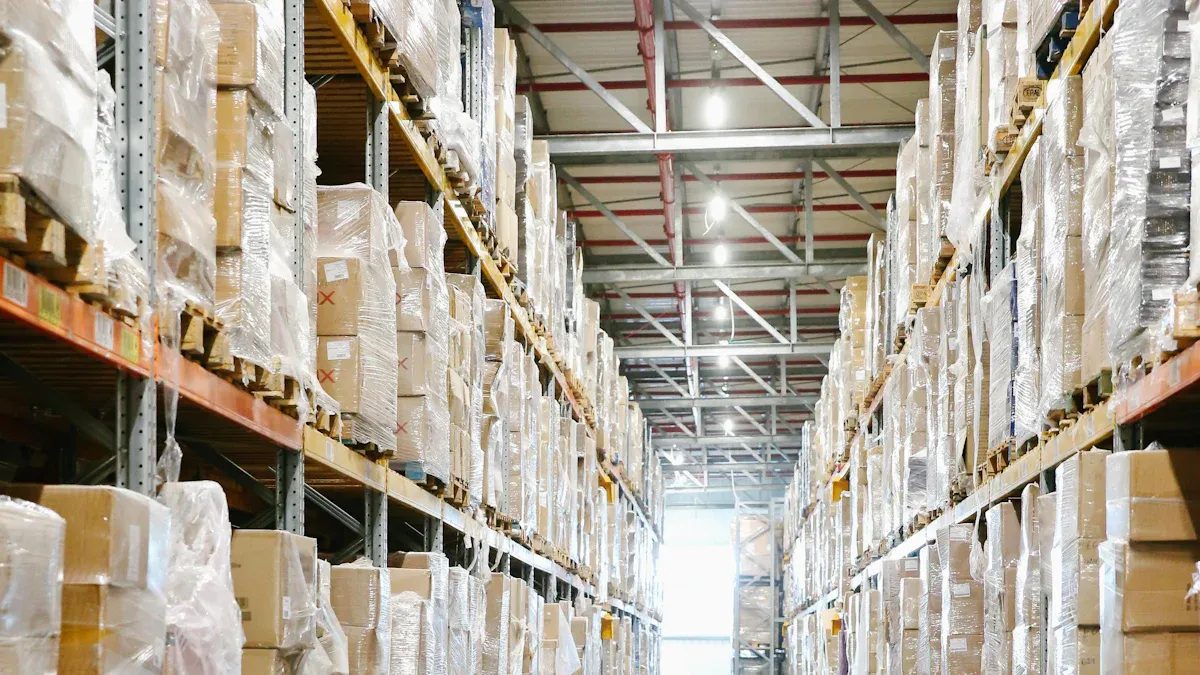
When you evaluate shelf labeling system options, you need to consider your operational environment, inventory dynamics, and long-term business goals. Each labeling method offers unique advantages for different retail and warehouse settings.
Paper and Synthetic Shelf Labeling
Durability and Cost Considerations
You often encounter two main material choices for shelf labeling: paper and synthetic (film) labels. Paper labels provide a cost-effective solution for controlled indoor environments. However, they tend to lose adhesion and durability when exposed to moisture, sunlight, or frequent handling. Over six months, paper facestocks can lose up to 30% of their stickiness in challenging conditions, leading to more frequent replacements.
Synthetic labels, such as BOPP or PET films, offer robust resistance to water, UV light, chemicals, and abrasion. These labels retain over 95% adhesion even with extended outdoor use. Although synthetic options have a higher upfront cost, they often reduce long-term expenses by minimizing the need for replacements in harsh environments.
Metric | Paper Facestocks | Film Facestocks |
---|---|---|
Adhesion Retention | Loses about 30% stickiness over 6 months under moisture and sunlight exposure | Retains over 95% adhesion even with extended outdoor use |
Durability | Prone to wrinkling, tearing, and water damage despite wet-strength treatments | Robust resistance to water, UV, heat, chemicals, and abrasion |
Cost | Lower upfront cost; may incur higher long-term replacement costs in harsh settings | Higher upfront cost; potential long-term savings due to fewer replacements |
Best-Use Scenarios for Each Material
You should use paper shelf labeling in retail environments with stable temperatures and low humidity. These labels work well for short-term promotions or areas with minimal handling. Synthetic labels excel in warehouses, cold storage, and outdoor retail displays. If your inventory faces frequent movement or exposure to harsh elements, synthetic labels maintain clarity and adhesion, supporting efficient operations.
Magnetic and Removable Warehouse Labeling
Flexibility for Dynamic Inventory
Magnetic and removable labeling systems give you unmatched flexibility. You can reposition these labels easily as inventory locations change. This adaptability proves essential in warehouses with high product turnover or seasonal inventory shifts. You avoid the hassle of scraping off old labels or damaging shelving surfaces.
- You can update storage locations quickly.
- You reduce downtime during inventory reorganizations.
- You maintain a clean, professional appearance on your shelves.
Ideal Applications in Warehouses
You benefit most from magnetic and removable shelf labeling in dynamic retail and warehouse environments. These systems support temporary storage, cross-docking, and areas where products rotate frequently. If your staff needs to reconfigure aisles or racks, magnetic labels streamline the process and minimize errors. Clear and consistent labeling of shelves and bins improves readability and accessibility, reducing mistakes and supporting efficient workflows.
Electronic Shelf Labeling (ESL) Solutions
Features, Benefits, and Limitations
Electronic shelf labeling systems transform how you manage pricing and inventory in retail and warehouse settings. These systems use digital displays—often E-ink or LCD—to present real-time product information. You can automate price updates across thousands of items, reducing manual labor and pricing errors. ESL solutions also support dynamic pricing, inventory tracking, and integration with warehouse management systems.
Market studies show that the electronic shelf labeling market reached $1.19 billion in 2024 and is projected to grow to $4.41 billion by 2033, with a CAGR of nearly 15%. Retailers and warehouses benefit from operational efficiency, reduced errors, and enhanced consumer experience. However, you must consider initial investment costs and integration complexity, which can challenge smaller operations.
Attribute | Data |
---|---|
Market Size (2024) | USD 1,194.7 Million |
Market Forecast (2033) | USD 4,413.6 Million |
CAGR (2025-2033) | 14.85% |
Key Drivers | Digital pricing, E-ink displays, wireless connectivity |
Applications | Retail, healthcare, logistics |
Benefits | Operational efficiency, inventory management, reduced errors, enhanced consumer experience |
Challenges | Initial costs, resistance to change |
You gain the ability to synchronize pricing and inventory data instantly, which supports faster decision-making and reduces selection errors. Research shows that clear, interpretive labeling—such as summary indicators—improves efficiency and accuracy in product selection, benefiting both staff and customers.
Choosing the Right ESL for Your Environment
When choosing the right ESL, you need to match the system’s features to your operational needs. E-ink displays offer excellent visibility and low power consumption, making them ideal for large retail floors and warehouses. LCD and LED options provide vibrant displays for high-traffic areas or promotional zones. You should assess your integration requirements, such as compatibility with inventory management software and wireless infrastructure.
If your business operates in regions with rapid retail growth, such as Asia-Pacific, you may find ESL adoption especially beneficial due to the demand for dynamic pricing and improved inventory management. You should also consider sustainability features, like bio-based ESL materials, to align with environmental goals.
Note: Electronic shelf labeling systems deliver significant operational benefits, but you must plan for the initial investment and ensure your staff receives proper training for a smooth transition.
Ensuring Label Durability and Readability
Selecting Materials for Longevity
Resistance to Environmental Stressors
You need to select labels that withstand the unique challenges of your warehouse. Labels face constant exposure to temperature changes, humidity, dust, and even chemicals. When you choose materials like freezer-grade synthetics or laminated surfaces, you protect your labeling from fading, peeling, or smudging. These materials keep your label readable and scannable, even in harsh environments. Durable labels reduce the need for frequent replacements, saving you time and money.
Adhesion and Fixing Methods
Proper adhesion ensures your labels stay in place. You should match the adhesive type to your shelving material and warehouse conditions. Permanent adhesives work well for long-term storage, while removable adhesives or magnetic backing suit dynamic inventory areas. Test your label on different surfaces before full-scale application. This step helps you avoid wasted labels and ensures your labeling system remains reliable.
Optimizing Readability and Identification
Font Size, Color Contrast, and Visibility
Clear labeling starts with readable text. Use large font sizes and high-contrast color combinations, such as black text on a white background. Good visibility helps your staff identify products quickly, even from a distance or in low-light areas. Place your label at eye level whenever possible. You can also use bold borders or colored backgrounds to highlight important information.
Use of Barcodes, QR Codes, and Alphanumeric Systems
Modern warehouse labeling relies on more than just text. Barcodes and QR codes allow for fast, accurate scanning and integration with inventory systems. You should ensure your label includes machine-readable codes alongside clear alphanumeric identifiers. This combination supports both manual picking and automated processes. When you use scan-friendly labels, you reduce errors and speed up order processing.
Maintaining Consistency in Warehouse Labeling
Standardized Design and Format
Consistency in your labeling design leads to fewer mistakes and faster workflows. Standardize your label format across all storage locations. Use logical location codes, such as aisle, bay, and level, to help staff find items quickly. Real-world case studies show that improving label design and placement can cut picking errors and speed up order fulfillment. Color-coded labels and large aisle markers further enhance navigation, especially during busy periods.
Label Placement for Maximum Visibility
Strategic placement of your labels makes a significant difference. Always position your label where staff can see and scan it without obstruction. Place labels at consistent heights and locations on racks or shelves. This approach reduces confusion and supports best practices for labeling. Integration with warehouse management systems and scanning technology can push your order accuracy rates close to 99.97%. Consistent labeling also prepares your warehouse for future automation, as robots and automated systems rely on clear, machine-readable codes.
Tip: Regularly audit your warehouse labeling to ensure all labels remain legible, properly placed, and up to date. This habit supports long-term efficiency and accuracy.
Planning Shelf Label Placement and Organization
Strategic Label Positioning
Eye-Level Placement and Multi-Level Indicators
You maximize visibility and accuracy when you position labels at eye level on each warehouse rack. Studies using eye-tracking technology show that centrally placed labels receive more attention and longer viewing times than those at the periphery or bottom. The table below highlights key findings from design research:
Aspect Evaluated | Key Findings |
---|---|
Label Position on Screen | Labels positioned centrally received more frequent and longer viewing than peripheral labels. |
Component Position on Label | Components near the top of the label were viewed more than those near the bottom. |
Implication | Eye-level (central) and top positioning enhances label visibility and consumer attention. |
You should use multi-level indicators for racks with several tiers. Place location labels at each level to help staff quickly identify the correct shelf. This approach reduces picking errors and supports maximum efficiency.
Avoiding Obstructions and Enhancing Accessibility
You improve warehouse efficiency when you avoid placing labels behind obstructions or in poorly lit areas. Ensure that every label remains visible from common approach angles. Use reflective or high-contrast warehouse rack labels in dim zones. When you label your racks with clear, accessible labels, you support fast scanning and reduce search time.
Logical Numbering and Coding Systems
Sequential, Categorical, and Serpentine Methods
A logical numbering system forms the backbone of any rack labeling strategy. You can use sequential numbering for straightforward aisles, categorical codes for product types, or serpentine methods for complex layouts. Research in inventory management shows that coding systems improve accuracy, monitoring, and reporting. You gain real-time status updates and standardized documentation, which leads to significant time and cost savings.
- Sequential: Assign numbers in order along each warehouse rack.
- Categorical: Use codes to group similar products or storage zones.
- Serpentine: Alternate numbering direction on each level for faster navigation.
Color Coding and Unique Identifiers
You enhance strategic labeling by adding color coding and unique identifiers to your warehouse rack labels. Color coding helps staff distinguish between zones or product categories at a glance. Unique identifiers, such as barcodes or QR codes, support automated scanning and tracking. Studies show that businesses using coherent coding systems see improved customer service and organizational performance.
Tip: Train your team on your chosen coding system. Consistent use of location labels and rack labeling ensures everyone can find items quickly.
Supporting Efficient Inventory Workflows
Minimizing Search and Restocking Time
Efficient labeling systems, including barcodes and RFID tags on warehouse rack labels, automate data capture and reduce errors. You enable real-time tracking and faster inventory counts. Retailers using these systems report a 30–50% reduction in stockouts and a 20% improvement in inventory accuracy. These gains directly minimize search and restocking time.
Streamlining Picking and Order Fulfillment
You streamline picking and order fulfillment when you label your racks with clear, scan-ready labels. Automated systems, such as Electronic Shelf Labels, provide real-time stock monitoring and alerts. This strategic labeling approach leads to faster turnaround times and helps improve warehouse efficiency. When you integrate location labels and rack labeling into your workflow, you support maximum efficiency and accuracy.
Integrating Shelf Labeling with Technology
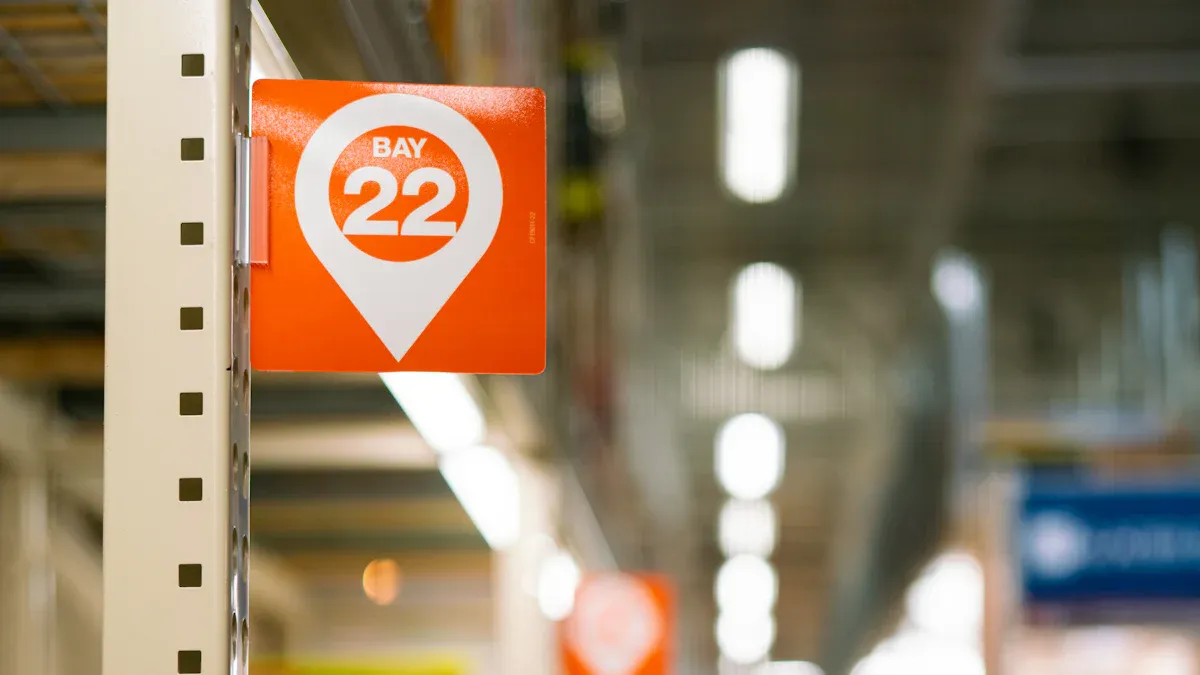
Compatibility with Inventory Management Systems
Software Integration and Data Synchronization
You gain the most value from your shelf labeling system when you integrate it with your inventory management software. Modern systems let you connect your labels directly to cloud-based platforms. This integration allows you to synchronize data across multiple warehouses and sales channels. You can automate stock tracking, which updates inventory levels as orders and shipments occur. This process reduces human error and eliminates the need for manual updates. You also benefit from automated alerts for low stock or discrepancies, which helps you manage inventory more proactively. Seamless integration with ERP, CRM, and e-commerce platforms ensures your labels always reflect accurate product information.
- Automated stock tracking for continuous updates
- Real-time access to inventory data from any location
- Automated alerts for low stock and discrepancies
- Synchronization with sales and financial records
Real-Time Updates and Tracking
You improve warehouse efficiency by using real-time updates and tracking. Cloud-based architecture lets multiple users access updated inventory data at the same time. Automated stock updates during transactions reduce manual errors and improve inventory accuracy. You can monitor stock levels instantly across all locations, which helps you avoid overselling and stockouts. Real-time data also supports better decision-making for replenishment and demand forecasting. Companies have seen a 25% reduction in stock discrepancies and a 30% faster order processing time after implementing real-time inventory tracking.
Implementing Barcodes, RFID, and Electronic Shelf Labeling
Benefits of Automated Inventory Tracking
You streamline your operations when you implement barcodes, RFID, and electronic shelf labeling. These technologies automate inventory tracking and reduce manual labor. Automated systems update your labels instantly as products move, which keeps your inventory records accurate. You can synchronize data across warehouses, POS, and e-commerce platforms. This approach leads to fewer errors, faster order fulfillment, and higher customer satisfaction. Automated inventory tracking also generates reorder alerts and purchase orders based on real-time data.
Choosing the Right Technology for Your Needs
You should evaluate your business size, inventory type, and operational needs before selecting a technology. Barcodes work well for most environments and offer a cost-effective solution. RFID labels provide faster scanning and bulk reading, which suits high-volume warehouses. Electronic shelf labeling offers dynamic updates and integration with digital systems. Choose the technology that aligns with your workflow and supports your long-term goals.
Scalability and Future-Proofing Your Shelf Labeling System
Adapting to Business Growth and Change
You need a shelf labeling system that adapts as your business grows. The enterprise labeling software market is expanding rapidly, driven by cloud-native architectures and hybrid deployment models. These features allow you to scale your labels and labeling processes quickly. Integration with ERP, supply chain, and IoT systems supports real-time updates and compliance workflows. Advances in AI and machine learning automate labeling, reduce errors, and embed regulatory compliance, making your system more adaptable.
Upgrading and Expanding Labeling Solutions
You future-proof your operations by investing in modular and hybrid shelf labeling designs. Over 30% of strategic investments now target digital shelf technology, including smart shelf features like electronic price tags and sensors. Modular systems let you adjust store layouts and expand your labeling as your needs change. Eco-friendly materials and smart shelving integration ensure your labels remain sustainable and scalable. These innovations help you improve warehouse efficiency and maintain high inventory accuracy as your business evolves.
Tip: Choose a shelf labeling system with open APIs and modular design. This approach ensures seamless integration and operational agility as your business grows.
Prioritizing Safety and Compliance in Warehouse Labeling
Including Safety Information and Load Limits
Clear Warnings and Hazard Labels
You protect your team and assets when you display clear warnings and hazard labels on every shelf. Labels should highlight risks such as flammable materials, heavy loads, or restricted access zones. Use bold colors and standardized symbols to draw attention. Place these labels at eye level and near potential hazards. This approach helps staff recognize dangers quickly and follow safety protocols. Consistent use of hazard labels reduces workplace accidents and supports a culture of safety.
Regulatory Compliance and Industry Standards
You must ensure your shelf labeling system meets all relevant regulations and industry standards. Regulatory bodies require you to display load limits, hazard warnings, and emergency instructions clearly. Labels should include information such as maximum weight capacity and handling precautions. Regular audits and inspections help you maintain compliance. You should review your labeling practices against OSHA, ANSI, and other applicable standards. Automation and real-time data capture through audit software improve consistency and help you meet operational standards. Frequent inspections—daily, weekly, or monthly—address immediate safety concerns and keep your warehouse compliant.
Documentation and Audit Readiness
Maintaining Accurate Records
You need to keep accurate records of your labeling system, safety checks, and compliance measures. Real-time documentation during audits captures observations and promotes transparency. Use digital tools to log label placements, updates, and maintenance activities. This practice ensures you can track changes and respond to issues quickly. Comprehensive training programs for audit personnel help your team understand checklist items and adapt to changing warehouse needs.
Preparing for Inspections and Audits
You prepare for inspections and audits by establishing clear procedures and regular review cycles. Pre-audit simulations familiarize your team with audit steps and reduce bottlenecks. Cross-functional audit teams bring diverse perspectives, which enhances the depth of evaluations. After each audit, interpret the data, create continuous improvement plans, and benchmark your performance against industry standards. Address common pitfalls, such as incomplete checklists or inadequate training, by reviewing processes and encouraging feedback. Regular warehouse audits and inspections identify inefficiencies and ensure ongoing compliance with safety and regulatory standards.
Tip: Schedule quarterly or biannual audits to review documentation, training records, and accident reports. Annual audits provide a comprehensive assessment of your warehouse’s performance and compliance.
Key Practices for Audit Readiness:
- Maintain real-time documentation for transparency.
- Conduct frequent inspections to address safety concerns.
- Use cross-functional teams for deeper evaluations.
- Implement post-audit feedback and continuous improvement plans.
By prioritizing safety information, regulatory compliance, and thorough documentation, you create a safer warehouse and support long-term operational excellence.
Choosing Reliable Shelf Labeling Suppliers and Support
Evaluating Vendor Quality and Product Reliability
Customer Reviews and References
You need to evaluate shelf labeling suppliers carefully to ensure consistent quality and reliable delivery. When you select a vendor for your labels, you should define clear criteria for comparison. These criteria include product quality, cost, delivery time, reputation, and customer service. Requesting references from current or previous clients helps you gather real feedback about the vendor’s performance and reliability. Customer reviews and references give you valuable insights into how well the supplier meets deadlines and resolves issues with label supply.
- Define your criteria: quality, cost, delivery time, reputation, customer service
- Request references from existing customers
- Review feedback on vendor performance and responsiveness
- Compare vendors using key metrics such as delivery time and customer service
- Validate claims by speaking directly with other businesses
Continuous evaluation of your label supply partners ensures you maintain high standards for your warehouse rack labels and retail operations.
Warranty and Replacement Policies
You should always review the warranty and replacement policies before finalizing your supplier. Reliable vendors offer clear guarantees on their labels, including coverage for defects or premature wear. A strong warranty protects your investment and reduces risk if you encounter issues with your warehouse rack labels. Replacement policies should be straightforward, allowing you to quickly resolve problems and avoid disruptions in your retail or warehouse workflow.
Assessing Support, Training, and Customization
Onboarding Assistance and Technical Support
You benefit from suppliers who provide comprehensive onboarding and technical support. Effective onboarding ensures your team understands how to use new labels and integrate them into your existing systems. Technical support helps you troubleshoot issues with label supply, printing, or application. Choose vendors who offer training resources, responsive customer service, and ongoing assistance. This support keeps your retail and warehouse operations running smoothly.
Custom Label Design and Regulatory Compliance
You may need custom label designs to meet specific business or regulatory requirements. Leading suppliers offer customization options for labels, including size, material, and print features. They also help you comply with industry standards for safety, traceability, and product information. When you work with a vendor who understands regulatory compliance, you reduce the risk of costly errors and ensure your retail labels meet all legal requirements.
Balancing Cost, Value, and Long-Term Investment
Upfront vs. Ongoing Costs
You must consider both upfront and ongoing costs when investing in a shelf labeling system. Upfront costs include hardware, software, and initial training. Ongoing costs cover maintenance, software updates, and technical support. The table below shows a typical cost breakdown for a comprehensive labeling solution:
Cost Category | Description | Amount (USD) |
---|---|---|
Capital Expenses | One-time investment in hardware/software | $200,000 |
HR (Development) | Initial integration and engineering time | $200,000 ($150K + $50K) |
Software License | Initial software purchase | $50,000 |
Training | Initial training for users | $10,000 |
Total Year 1 Cost | Sum of all upfront costs | $460,000 |
HR (Ongoing) | Annual technician and model tuning | $50,000 ($20K + $30K) |
Software Maintenance | Annual software upkeep | $10,000 |
Total Annual Ongoing | Sum of recurring yearly costs | $60,000 |
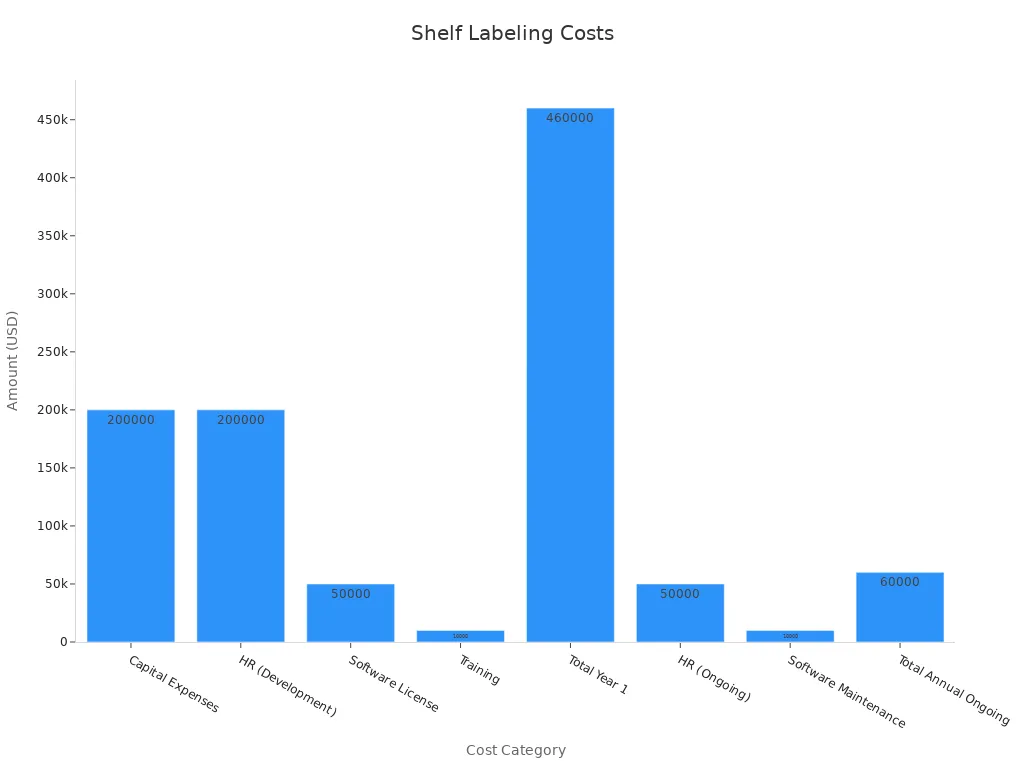
Cost-benefit analysis frameworks, such as Net Present Value (NPV) and Return on Investment (ROI), help you compare these expenses with the expected benefits. For example, if your labeling system generates $300,000 in annual benefits, you can achieve payback in about two years. This approach ensures you make informed decisions about your label supply and technology investments.
Scalability and Return on Investment
You should select a supplier who can scale with your business as it grows. Scalable solutions allow you to expand your labels across new retail locations or warehouse zones without major disruptions. Evaluate the long-term value by considering how the system supports future upgrades, regulatory changes, and increased demand for labels. A reliable supplier helps you maximize ROI by providing durable, adaptable labels that support your evolving needs in both retail and warehouse environments.
Tip: Prioritize suppliers who offer transparent pricing, flexible support, and proven reliability. This strategy ensures your investment in labels delivers value for years to come.
You ensure inventory management success when you follow a structured approach to shelf labeling. Assess your inventory, select the right system, and focus on durability, readability, and integration. Consider these proven benefits:
- Durable, environment-appropriate labels maintain visibility and reduce errors.
- Integration with inventory software streamlines tracking and boosts accuracy.
- Clear, consistent labeling minimizes picking mistakes and increases productivity.
- Strategic placement and advanced techniques optimize workflow and safety.
Investing in the right shelf labeling system supports efficiency, accuracy, and long-term business growth.
FAQ
What is the most durable material for shelf labels?
Synthetic materials, such as BOPP or PET film, offer the highest durability. These labels resist water, chemicals, and abrasion. You can use them in harsh environments, including cold storage and outdoor areas.
How often should you update or replace shelf labels?
You should inspect labels quarterly. Replace any that show wear, fading, or peeling. In high-turnover areas, update labels whenever you move products or change inventory locations.
Can you integrate shelf labels with inventory management software?
Yes. Most modern shelf labeling systems support integration with inventory management software. You can automate updates, synchronize data, and track inventory in real time.
What are the benefits of using color-coded shelf labels?
Color-coded labels help you organize products by category, zone, or priority. You can reduce picking errors and speed up navigation. Staff can identify sections quickly, improving workflow efficiency.
Are electronic shelf labels (ESL) suitable for small businesses?
You can use ESL in small businesses, but consider the initial investment. ESL offers real-time updates and automation. If you need frequent price changes or inventory tracking, ESL can provide long-term value.
How do you ensure shelf labels remain readable in low-light areas?
Use high-contrast colors and large fonts. Place labels at eye level and add reflective or illuminated options if needed. You can also conduct regular visibility checks to maintain readability.
What is the best way to train staff on a new shelf labeling system?
Provide hands-on training sessions. Use clear guides and visual aids. Encourage staff to practice scanning and locating items. Regular refresher courses help reinforce best practices.
Can you reuse shelf labels when reorganizing inventory?
You can reuse magnetic or removable labels. These options allow you to reposition labels without damaging shelves. For permanent adhesive labels, you should use new ones to maintain clarity and adhesion.