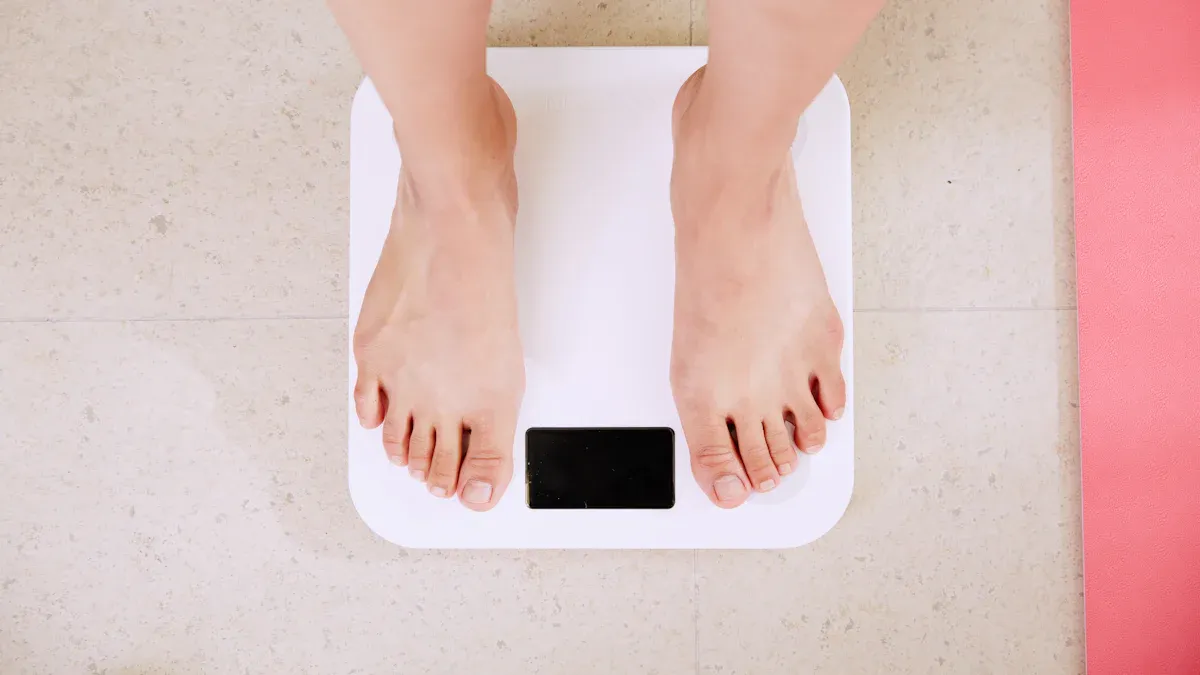
Selecting the right digi scale for your business starts with understanding your weighing scale needs. You should consider how accuracy impacts your daily processes. Each scale offers unique features for weighing different products, whether you run an Esl Retail shop or manage inventory with Electronic Shelf Labels. Many businesses benefit from an ESL Gateway AP or an ESL Price Tag to streamline operations. When you choose the proper scales, you improve efficiency and reliability.
Identify Your Business Needs for the Right Weighing Scales
Selecting the right weighing scales starts with a clear understanding of your business requirements. You need to analyze what you weigh, where you use the scales, and how they fit into your daily operations. This approach ensures you choose a weighing solution that supports accuracy and efficiency.
Define What You Need to Weigh
Product Types and Sizes
You should first identify the types of items you plan to weigh. Different products require different types of weighing scales. For example, if you handle bulk goods, you need commercial scales with higher capacity. If you sell small packaged items, you need scales with fine precision. Consider the size of your products. Large items may need platform scales, while small goods fit better on compact models.
Tip: Make a list of your most common products and their average size. This step helps you match your needs to the right scale.
Packaging and Handling Requirements
Packaging affects how you use your scales. If your products come in boxes, bags, or containers, you need to check if the scale platform can support them. Some scales offer features like tare functions, which let you subtract the weight of packaging. You should also think about how you handle products. If you move items often, choose a scale that is easy to load and unload.
Assess Where the Weighing Scales Will Be Used
Retail, Industrial, or Food Service Environments
Your business environment shapes your choice of weighing scales. Retail stores need user-friendly scales for fast transactions. Industrial settings require durable models that handle heavy loads. Food service businesses need hygienic scales that meet safety standards. Each environment has unique demands, so match your scale to your setting.
Space and Mobility Considerations
Space plays a key role in your decision. Measure the area where you plan to place your scales. Compact spaces need small, portable models. If you move your scales between locations, look for lightweight designs with handles or wheels. Mobility ensures you can adapt to changing workflows.
Understand How the Scale Fits Your Workflow
Frequency and Volume of Use
Think about how often you use your scales and the volume of items you weigh. High-traffic businesses need robust scales that withstand constant use. If you weigh items only a few times a day, a basic model may be enough. Frequent use calls for reliable, easy-to-clean designs.
Integration with Existing Processes
Your scales should fit smoothly into your current workflow. Check if the scale connects to your point-of-sale system or inventory software. Integration saves time and reduces errors. Some scales offer digital displays or data export features, making it easier to track weights and manage records.
Note: Choosing the right weighing scales involves more than just picking a model. You need to match the scale’s features to your business requirements, product size, and workflow.
Determine Accuracy and Capacity for the Ideal Scale for Your Retail Business
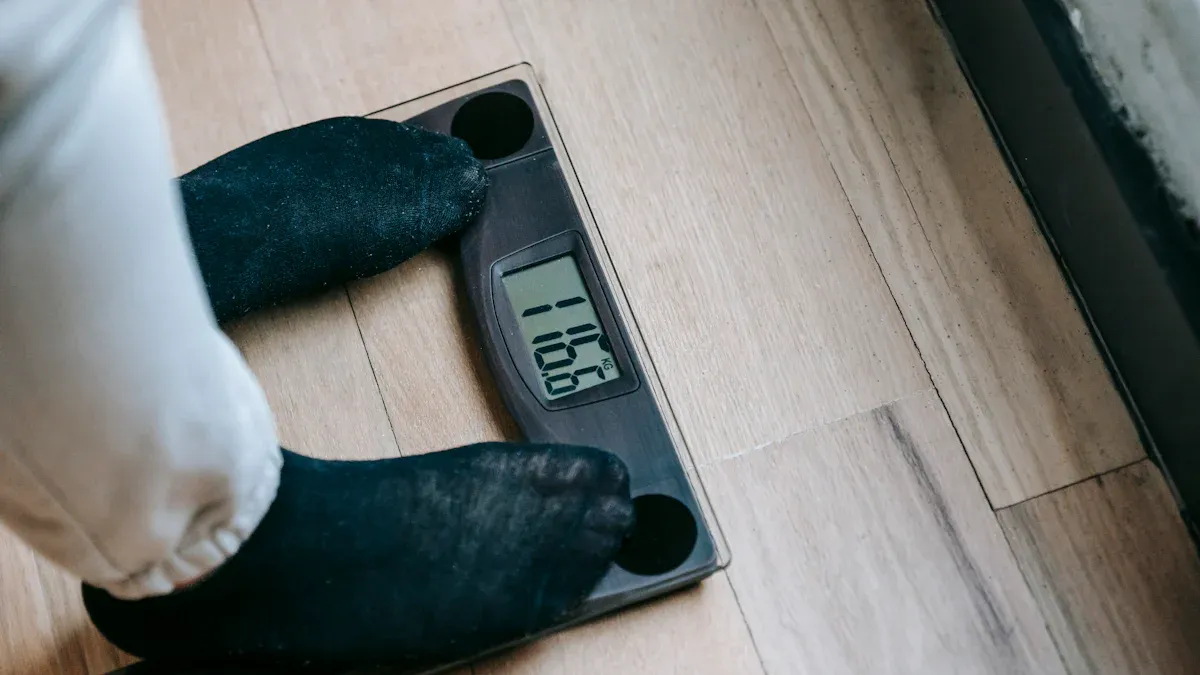
Selecting the right weighing scale for your business requires a close look at both accuracy and weighing capacity. These two factors ensure you meet legal standards, protect your investment, and deliver reliable results every day.
Precision and Readability Requirements
Minimum Increments and Sensitivity
You need a weighing scale that delivers precise measurements for every transaction. The minimum increment, or readability, tells you the smallest weight change the scale can detect. For example, if you sell spices or jewelry, you need a scale with high sensitivity and fine increments. In retail, even small errors can add up over time, so accuracy matters.
Modern weighing scales use advanced technology to achieve high precision. Electromagnetic Force Compensation (EMFC) weighing cells and automatic internal adjustment systems, such as FACT, help maintain consistent accuracy. These features allow your scale to adapt to temperature changes and other environmental factors, so you always get reliable readings.
Tip: Choose a scale with a readability that matches your product type. Overly sensitive scales may slow down your workflow, while low-sensitivity models can lead to costly mistakes.
Legal-for-Trade and Compliance Standards
You must ensure your weighing scale meets legal-for-trade requirements. Compliance with standards like OIML and NTEP guarantees your scale provides accurate and repeatable results. Certified scales support your business in meeting regulatory demands and help you avoid fines or disputes.
Routine calibration and testing are essential. Many modern scales offer integrated firmware for automatic routine testing, user management, and activity logs. These features help you maintain compliance and simplify audits.
Feature Category | Details |
---|---|
Overload Protection | Safeguards weighing cell against excess loads and accidental drops on the weighing pan. |
Precision Technology | Electromagnetic Force Compensation (EMFC) weighing cell; FACT automatic internal adjustment. |
Compliance Standards | OIML/NTEP approved, ensuring legal-for-trade precision benchmarks. |
Quality Assurance | User management, leveling assistant, configurable sample/task IDs, activity log, routine tests. |
Durability | Full metal housing tested in harsh environments for protection against dirt and chemicals. |
Weight Capacity and Overload Protection
Maximum Load Limits
You must match the weighing capacity of your scale to your typical product loads. The weighing capacity tells you the maximum weight the scale can handle without damage or loss of accuracy. If you often weigh heavy items, select a scale with a higher maximum load limit. For lighter products, a lower capacity scale may offer better precision.
Overloading a scale can cause permanent damage and reduce accuracy. Manufacturers publish overload protection values to show how much extra weight the scale can withstand. This feature protects your investment and ensures long-term reliability.
Safety Margins for Typical Loads
Always consider a safety margin when choosing your ideal scale for your retail business. Select a model with a weighing capacity that exceeds your heaviest expected load. This approach prevents accidental overloads and extends the life of your equipment.
You can look for these features in modern weighing scales:
- Overload protection that guards the weighing cell from accidental drops or excess weight.
- MonoBlocHighSpeed weighing cells for fast, precise measurements.
- FACT automatic internal adjustment for consistent accuracy.
- Certified models for legal-for-trade use and statistical applications.
Acceptable precision in commercial weighing scales depends on reproducibility. Your scale should provide consistent readings, even with temperature changes or after repeated use. Regular calibration, clear overload protection values, and compliance with standards ensure your weighing scale remains reliable.
Note: Investing in the right weighing scale with proper weighing capacity and overload protection helps you avoid costly downtime and supports smooth business operations.
Match DIGI Scale Features to Your Business Environment
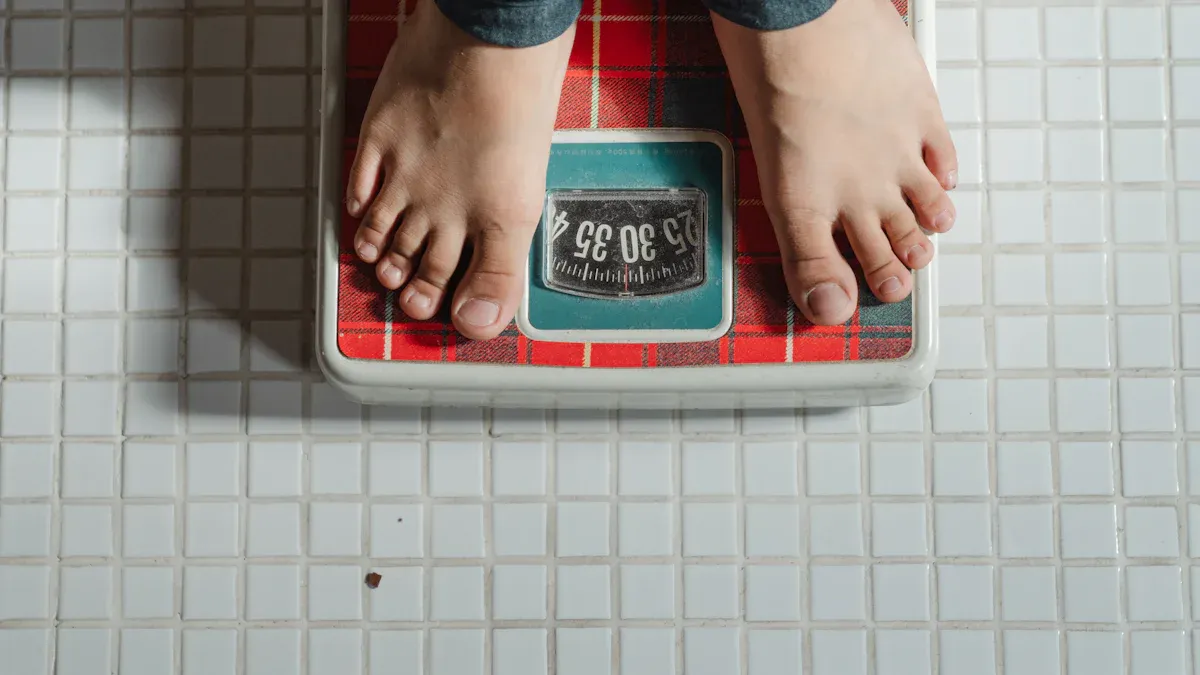
Durability and Build Quality of Weighing Scales
Material Construction and Resistance
You need a digi scale that stands up to daily use. Manufacturers design high-quality weighing scales with robust materials like stainless steel or reinforced plastic. These materials resist corrosion, dents, and scratches. When you choose a scale with solid construction, you protect your investment and reduce downtime. Look for models that offer sealed buttons and reinforced frames. These features help your weighing scale last longer in demanding environments.
Suitability for Frequent Cleaning and Handling
Retail and food service businesses often require frequent cleaning. You should select scales with smooth surfaces and minimal crevices. This design makes cleaning quick and prevents residue buildup. Some weighing scales feature removable pans or waterproof housings. These options allow you to sanitize your equipment without damaging sensitive components. If your team handles the scale often, choose a lightweight model with ergonomic grips. This approach reduces the risk of drops and extends the life of your equipment.
Tip: Regular cleaning and careful handling help maintain the quality and accuracy of your digi scale.
Environmental Protection and Adaptability
Waterproof, Dustproof, and Temperature Tolerance
Your business environment may expose your scales to moisture, dust, or temperature changes. Many high-quality digi scale models come with IP ratings that indicate resistance to water and dust. For example, an IP65-rated weighing scale can handle splashes and dust without losing accuracy. If you operate in a cold storage area or a hot kitchen, check the temperature tolerance range. This information ensures your scales deliver reliable results in any condition.
Performance in Challenging Conditions
You may need to use your weighing scales in environments with vibration, humidity, or chemical exposure. Choose a digi scale with a sealed housing and chemical-resistant surfaces. These features protect sensitive electronics and maintain measurement quality. Some scales include shock-absorbing feet or anti-slip bases. These additions help your weighing scale stay stable and accurate, even on uneven surfaces.
Display and User Interface Options
Readability in Various Lighting Conditions
You want your team to read measurements quickly and accurately. Modern digi scale displays use bright LCD or LED screens. These displays remain clear in both bright and dim lighting. Some weighing scales offer adjustable backlighting, which improves visibility in different settings. A clear display reduces errors and speeds up your workflow.
Touchscreen vs. Button Controls
You can choose between touchscreen and button controls for your digi scale. Touchscreens provide a modern look and allow for easy navigation. Button controls offer tactile feedback and work well in environments where gloves are required. Comparative studies show that interfaces designed with usability principles—such as at-a-glance layouts—score higher in user confidence and perceived usability. For example, a study found that at-a-glance interfaces achieved a System Usability Scale score of 81, compared to 51 for guided navigation interfaces. Users also reported higher confidence levels with usability-focused designs. However, accuracy rates remained similar between both types.
Metric | Guided Navigation | Usability Principles (At-a-Glance) |
---|---|---|
SUS Score | 51 | 81 |
Accuracy Rate | ~64.3% | ~68.9% |
Confidence Level | 80.7% | 88.8% |
You should select the interface that best fits your workflow and staff preferences. A user-friendly interface supports efficiency and helps maintain the quality of your weighing process.
Consider Essential Functions and Technology in DIGI Scales
Digital vs. Analog Weighing Scales
Pros and Cons for Business Operations
You face a choice between digital and analog weighing scales. Each option brings unique strengths and limitations to your business operations.
- Digital scales improve quality control and automate repetitive tasks. You can rely on them to minimize waste and support sustainability by optimizing resource use.
- Digital models enable advanced data collection and transfer. You gain access to USB, Ethernet, and WiFi connectivity, which allows real-time data logging and remote monitoring.
- These features streamline your workflow and help you meet industry standards.
- Analog scales offer simplicity and require less technical knowledge. However, they lack the automation and integration capabilities that digital models provide.
Tip: Digital scales support portion control, consistency, and safety in industries like food and chemical production. You can achieve higher operational efficiency and better compliance with these features.
Suitability for Your Sector
You should match your choice of scales to your sector’s needs. Retail and food service businesses benefit from digital scales because they offer automatic data capture and integration with management systems. Industrial environments may still use analog models for basic tasks, but digital options deliver greater flexibility and control. If your business requires precise tracking, reporting, or compliance, digital scales provide the best fit.
Connectivity and System Integration
POS and Inventory Management Compatibility
You can enhance your business by choosing scales that integrate with your point-of-sale (POS) and inventory management systems. Integrated weighing sensors allow you to monitor inventory levels in real time, even from remote locations. This capability prevents stockouts and ensures you always have the right products on hand.
- Real-time digital communication keeps your inventory data accurate.
- Weight sensors improve pick and pack accuracy, reducing costly errors.
- You can track materials that are difficult to manage with traditional methods.
Wireless, Data Export, and Software Features
Modern scales offer wireless connectivity, data export, and software integration. You can monitor inventory at the point of use, whether on the production floor or in storage. Intelligent dispensing solutions and mobile racks with wireless features save time and improve accountability. These combined features lead to significant cost savings and better inventory visibility.
Feature | Benefit |
---|---|
Wireless Connectivity | Flexible, real-time monitoring |
Data Export | Easy record-keeping and compliance |
Software Integration | Seamless workflow and reporting |
Additional Features for Efficiency
Label Printing and Barcode Scanning
You can boost efficiency by selecting scales with built-in label printing and barcode scanning. These features speed up checkout, improve traceability, and reduce manual entry errors. Your staff can print labels directly from the scale, making product identification and inventory management easier.
Tare, Zero, and Counting Functions
Essential functions like tare, zero, and counting help you handle complex weighing tasks. The tare function lets you subtract container weight, ensuring you measure only the product. The zero function resets the scale, while counting functions simplify inventory tasks by quickly tallying identical items. These automatic features save time and reduce mistakes in your daily operations.
Note: When you choose weighing scales with advanced technology and essential functions, you set your business up for greater accuracy, efficiency, and growth.
Set Your Budget and Evaluate Value When Choosing Weighing Scales
Balancing Cost and Quality
Upfront Price vs. Long-Term Savings
When you evaluate weighing scales for your business, you may feel tempted to focus on the lowest upfront price. However, you should consider the long-term savings that come from investing in a reliable, high-quality scale. A cheaper model might seem attractive at first, but frequent repairs, downtime, or inaccurate measurements can quickly erode any initial savings. You can protect your bottom line by choosing a scale that delivers consistent performance and durability. Over time, a dependable scale reduces maintenance costs and supports smooth operations.
Tip: Calculate the total cost of ownership, not just the purchase price. This approach helps you see the real value of your investment.
Warranty, Service, and Support
You should always check the warranty and support options before making a purchase. A strong warranty signals that the manufacturer stands behind the quality of their product. Reliable service and support ensure that you can resolve issues quickly, minimizing disruptions to your business. Look for suppliers who offer clear service agreements, fast response times, and easy access to replacement parts. These factors contribute to the overall value of your weighing scale and help you maintain high standards in your daily operations.
Investment and Scalability
Planning for Business Growth
As you plan your investment, think about how your business might grow in the future. Scaling your operations means increasing revenue and profitability without a matching rise in costs. When you choose scalable weighing solutions, you set your business up to handle more volume efficiently. Automation, modular designs, and standardized processes allow you to expand without needing to buy entirely new equipment. This strategy supports sustainable growth and gives you a competitive edge in your market.
Scalable operations let you serve larger markets and adapt to changing demands. Many investors look for scalability because it shows your business can achieve exponential returns. By planning for growth now, you avoid costly upgrades later and ensure your weighing systems keep pace with your success.
Total Cost of Ownership
You should evaluate the total cost of ownership when selecting a weighing scale. This calculation includes the purchase price, maintenance, calibration, and potential upgrades. A high-quality scale may cost more upfront, but it often requires less maintenance and lasts longer. You benefit from fewer interruptions and more accurate results. Consider how your choice will impact your business over several years, not just at the point of sale.
Cost Factor | Short-Term Impact | Long-Term Impact |
---|---|---|
Purchase Price | Immediate | One-time |
Maintenance | Low/Medium | Recurring |
Calibration | Low | Recurring |
Upgrades | None/Low | Possible, as you grow |
Downtime | Low | Reduced with quality |
Note: Investing in scalable, high-quality weighing scales supports your business as it grows and helps you manage costs effectively.
Test and Verify the Ideal Scale for Your Retail Business Before Purchase
Request Demos and Hands-On Trials
Testing with Your Actual Products
You should always request a demo or hands-on trial before you commit to a weighing scale. Testing the scale with your actual products gives you a clear picture of how it performs in real-world conditions. Place your most common items on the scale and observe the accuracy, speed, and stability of the readings. This process helps you identify any limitations or unexpected issues. You can also check if the scale accommodates your packaging and fits your workspace.
Tip: Bring a sample set of your products to the demo. This step ensures the scale meets your specific needs and handles your daily workflow.
Evaluating Ease of Use and Workflow Fit
Ease of use plays a critical role in daily operations. During your trial, pay attention to the user interface, display clarity, and control layout. You want a scale that your staff can operate confidently, even during busy periods. Test common functions like tare, zero, and counting. Evaluate how quickly you can switch between modes or print labels. A scale that fits your workflow reduces training time and minimizes errors.
You can use a simple checklist to guide your evaluation:
Feature | Meets Needs | Notes |
---|---|---|
Accurate Readings | ✅ | |
Fast Response Time | ✅ | |
Easy to Clean | ✅ | |
User-Friendly Display | ✅ | |
Integration Options | ✅ |
Assess Supplier Support and Reputation
Training, After-Sales Service, and Maintenance
Supplier support extends far beyond the initial purchase. You should look for suppliers who offer comprehensive training, responsive after-sales service, and regular maintenance. Reliable support ensures your scale stays accurate and compliant with industry standards. Regular calibration and maintenance, provided by a dependable supplier, protect your business from costly errors and legal risks. When you have access to expert help, you can resolve issues quickly and keep your operations running smoothly.
Customer satisfaction metrics, such as the Customer Satisfaction Score (CSAT), highlight the value of robust supplier support. High CSAT scores reflect positive experiences with both the product and the service. When your supplier provides consistent support, you benefit from greater reliability and fewer disruptions. The Customer Satisfaction Index (CSI) also measures how well suppliers meet your needs across all touchpoints, including product performance and support. Strong supplier relationships lead to higher CSI scores and greater customer loyalty.
Note: Reliable supplier support directly impacts your scale’s accuracy, compliance, and your customers’ trust in your business.
Customer Reviews and References
You should research supplier reputation before making a final decision. Read customer reviews and ask for references from businesses similar to yours. Reviews often reveal how suppliers handle challenges, respond to service requests, and support their clients over time. Positive feedback signals a trustworthy partner who values long-term relationships. When you choose a supplier with a strong reputation, you gain confidence in your investment and reduce the risk of future problems.
Remember: A supplier’s track record for support and service is just as important as the features of the scale itself. Choose partners who help you succeed now and as your business grows.
Quick Checklist for Selecting the Right DIGI Scale
Step-by-Step Summary for Choosing Weighing Scales
Selecting the right DIGI scale requires a systematic approach. Use this checklist to guide your decision and ensure you cover every critical aspect.
Needs Assessment
- List Your Products: Write down the main items you plan to weigh. Include their average sizes and packaging types.
- Define Your Environment: Identify where you will use the scale—retail, industrial, or food service. Note any special requirements, such as hygiene or mobility.
- Clarify Workflow Demands: Determine how often you will use the scale and how it fits into your daily operations.
Tip: A clear needs assessment helps you avoid costly mistakes and ensures the scale supports your business goals.
Feature and Environment Matching
- Compare Scale Features: Match the scale’s capacity, precision, and functions to your product list.
- Check Durability: Select materials and build quality that withstand your environment. Stainless steel suits food service, while reinforced plastic works well in retail.
- Evaluate Environmental Protection: Look for IP ratings if you expect exposure to water or dust. Confirm temperature tolerance for cold or hot settings.
- Assess User Interface: Choose between touchscreen and button controls based on your staff’s preferences and workflow.
Feature | Why It Matters |
---|---|
Capacity & Precision | Ensures accurate measurements |
Durability | Reduces downtime |
Environmental Rating | Protects against damage |
Display Type | Improves usability |
Budget and Value Review
- Calculate Total Cost: Consider not only the purchase price but also maintenance, calibration, and potential upgrades.
- Review Warranty and Support: Choose suppliers who offer strong warranties and responsive service.
- Plan for Growth: Select scalable solutions that can grow with your business.
Note: Investing in quality now saves you money and trouble in the long run.
Testing and Supplier Evaluation
- Request a Demo: Test the scale with your actual products. Check for accuracy, speed, and ease of use.
- Evaluate Supplier Support: Ask about training, after-sales service, and maintenance options.
- Research Reputation: Read independent reviews and request references from similar businesses.
Checklist Table:
Step | Completed (✔/✗) | Notes |
---|---|---|
Needs Assessment | ||
Feature & Environment Match | ||
Budget & Value Review | ||
Testing & Supplier Eval |
Use this checklist as you move through the selection process. You will make a confident, informed choice that supports your business now and in the future.
Choosing the right DIGI scale requires you to match your business needs with the scale’s features, accuracy, and value. Use the checklist and steps in this guide to make a confident, informed decision.
Remember: The ideal scale supports your operations today and adapts as your business grows. Invest wisely to ensure long-term efficiency and reliability.
FAQ
What is the difference between a legal-for-trade scale and a standard scale?
A legal-for-trade scale meets government standards for accuracy. You can use it for commercial transactions. Standard scales may not meet these requirements. Always check certification before using a scale for sales.
How often should you calibrate your DIGI scale?
You should calibrate your scale regularly. Most businesses calibrate monthly or after moving the scale. Follow the manufacturer’s recommendations for best results.
Can you connect a DIGI scale to your POS system?
Yes, many DIGI scales offer POS integration. You can connect them using USB, Ethernet, or wireless options. This feature streamlines checkout and inventory management.
What does the IP rating on a scale mean?
The IP rating shows how well your scale resists dust and water. For example, IP65 means your scale can handle dust and low-pressure water jets. Always choose a rating that matches your environment.
Do you need special training to use a digital weighing scale?
Most digital scales have user-friendly interfaces. You can learn basic functions quickly. For advanced features, you may need short training sessions. Many suppliers offer guides or tutorials.
What should you do if your scale shows inaccurate readings?
First, check for debris or uneven surfaces. Clean the scale and ensure it sits flat. If problems continue, recalibrate the scale. Contact your supplier if you still see errors.
Which features help you save time during busy hours?
Look for features like fast stabilization, label printing, and barcode scanning. These options speed up weighing and checkout. You can also use preset tare functions for common containers.
Tip: Always review your workflow to identify which features will boost your team’s efficiency.